Formulation Development for Surface Coatings
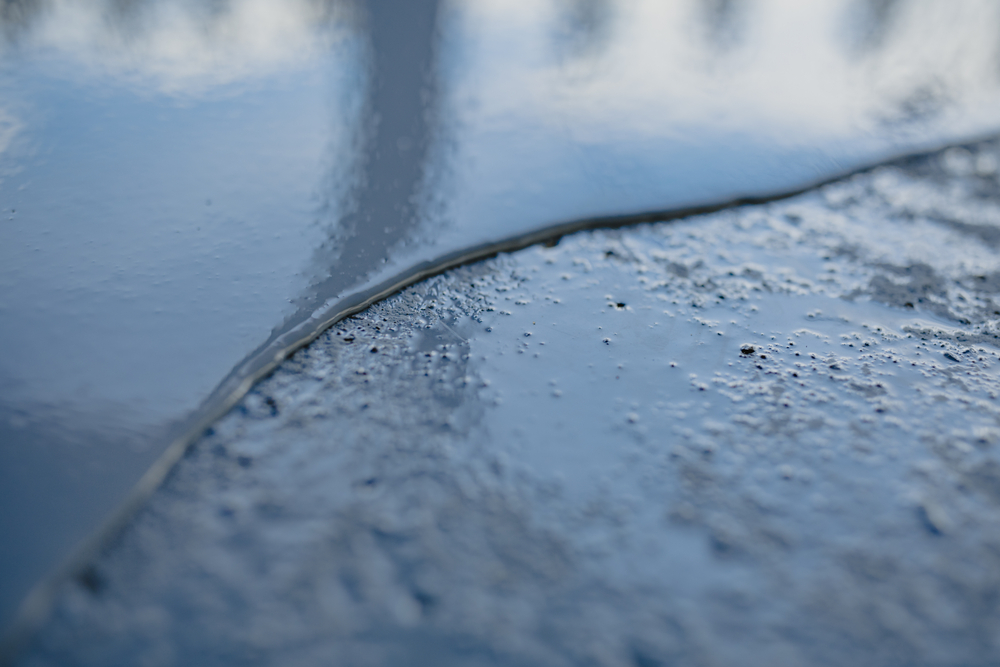
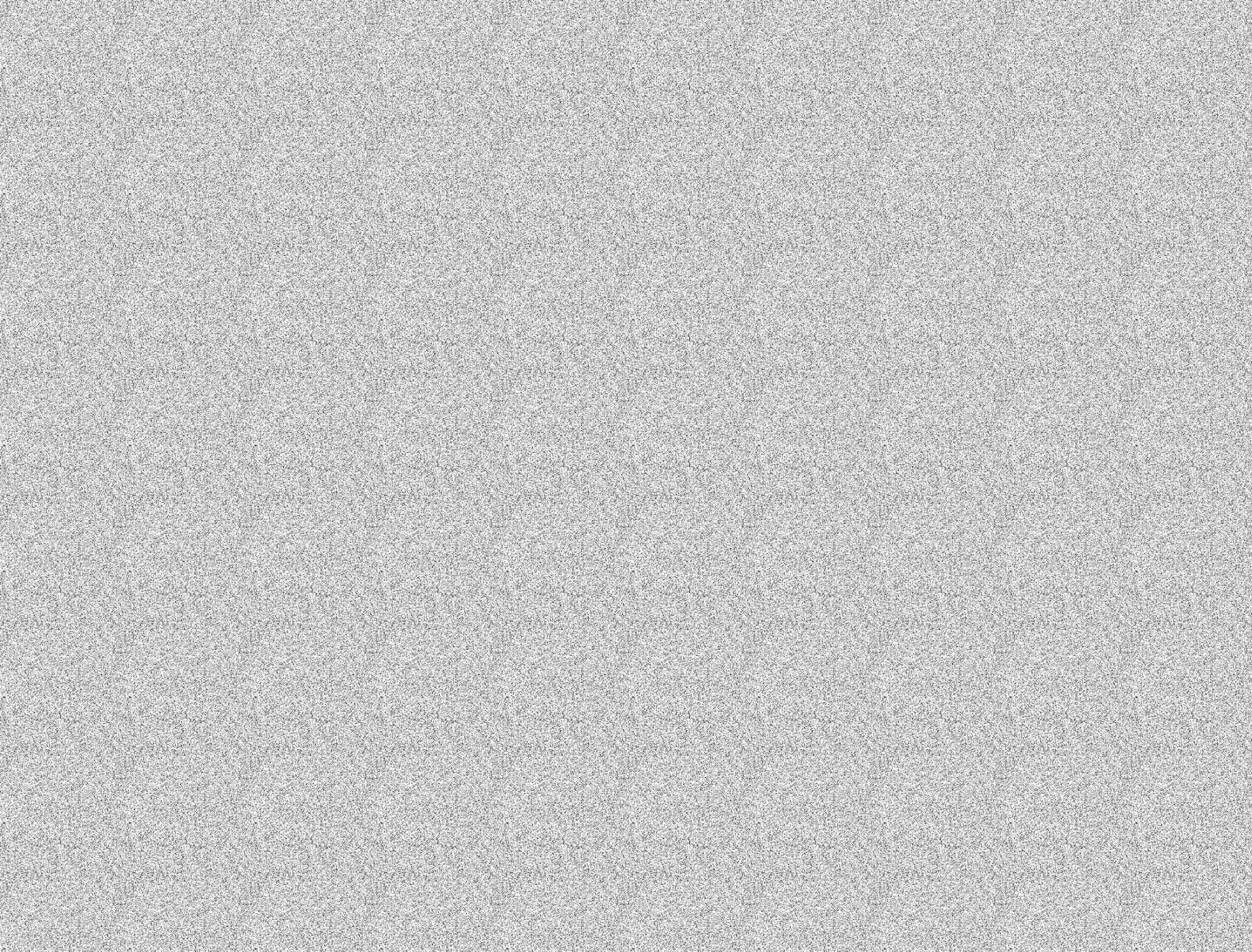
Intro
Formulation development in surface coatings faces significant challenges due to the need to optimize multiple properties, manage extensive raw material inventories, and frequently reformulate existing products in response to regulatory and market demands. Compounding these issues are data management difficulties, with crucial materials data often fragmented and inaccessible across various systems. The MaterialsZone all-in-one materials informatics platform streamlines these processes by consolidating data into an accessible, AI/ML-ready format. It offers advanced tools like the Visual Analyzer and Predictive Co-Pilot to enhance data-driven decision-making, optimize formulations, and accelerate R&D cycles, enabling faster reformulation and innovation in the surface coatings industry.
Inherent Challenge
Paints and coatings are characterized by tens of properties that require parallel optimization. A single manufacturing site keeps over 2000 raw materials to sustain thousands of products for various applications. The R&D and manufacturing processes are long and typically involve milling, synthesis, mixing, dispersing, let down, tests, and filling. In addition to this, R&D teams are required to reformulate hundreds of existing products annually because of several triggers (regulation, cost, supply chain, and market demand). These reformulations leave little space for experimenting with new formulations, let alone the discovery and development of new products as R&D teams are caught in an endless cycle of meeting urgent market demands.
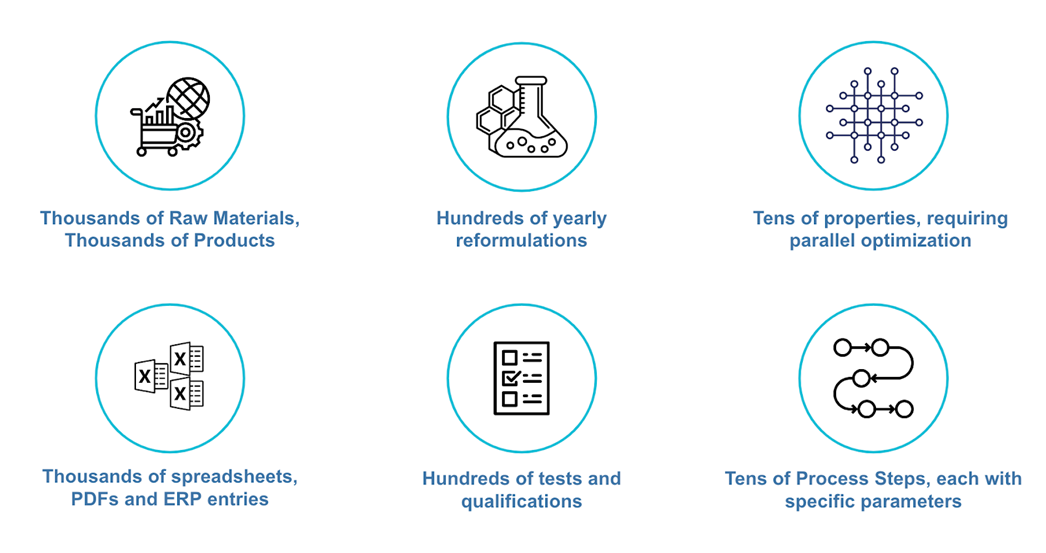
Data Challenge
In addition to the inherent challenges within Paints and Coatings R&D, researchers also face the added difficulty of data aggregation and management. Raw materials data may be managed within the organization's ERP system, or documented in a department’s local spreadsheets or PDFs. The result is that much of an organization’s materials data is lost or inaccessible, meaning that R&D teams struggle to make data-driven decisions with regard to raw material selection. Furthermore, procurement, regulation, and safety personnel are responsible for the materials knowledge pertaining to their domains. This makes the pain of quickly reacting to regulatory changes even more severe, as the data may be inadequately documented or not readily available for merging with R&D or production data.
Lastly, due to the difficulty of documenting experimental results with systems that were not designed specifically for this purpose (such as ERP or Product Life Cycle tracking software), R&D teams end up documenting only operational formulations, meaning that experimental iterations—and the knowledge and insights gained from them—are often lost.
MaterialsZone Solution for Surface Coatings Formulations
MaterialsZone’s solution to these challenges brings the strengths of an all-in-one materials informatics platform for accelerating R&D cycles within the Surface Coatings industry.
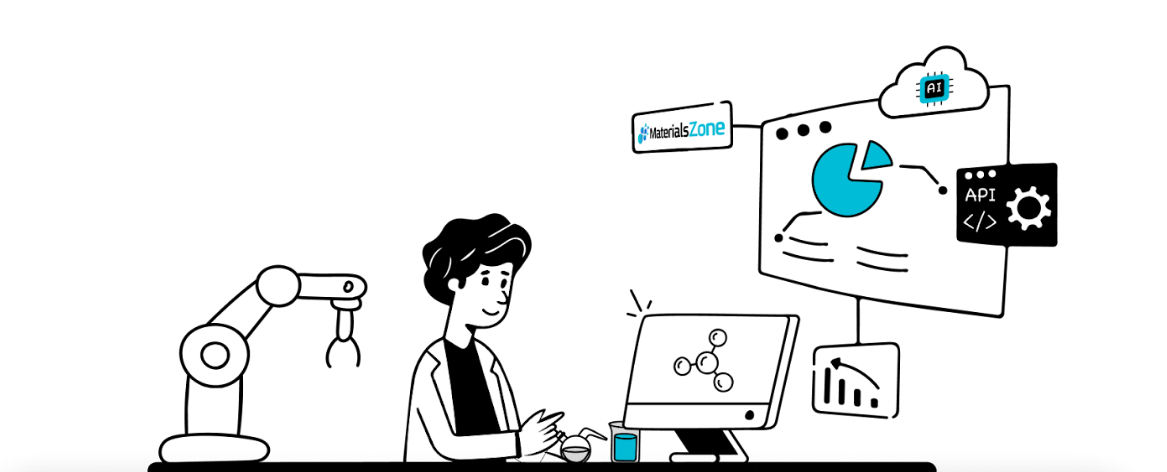
Data Consolidation
MaterialsZone’s Materials Knowledge Center has the ability to consolidate and centralize all of an organization’s materials data in one place, making it both accessible and AI/ML ready for analysis by all relevant stakeholders. The data is searchable by keywords, and attributes, and can be easily filtered by product requirements so that researchers have the information they need at their fingertips. The data is structured in an intuitive way that can be navigated by categories, designed to fit the teams’ needs.
For example, some raw materials categories are:
- Pigments (inorganic pigments, organic pigments, dyes)
- Binders (resins, polymers)
- Solvents (vehicles, diluents)
- Additives (dispersing agents, leveling agents, defoamer, biocide, fungicide, antislip, thickeners, corrosion inhibitors, matting agents, etc.)
- Packaging
In addition to technical attributes and linkages to their end uses, the materials can be further enriched with Safety and Regulation Data, and material properties can be aggregated at light speed using advanced GenAI capabilities, allowing teams to use this extra layer of information within their searches, visualizations, and AI/ML models.
Formulations, processes, and product requirements can be linked within the platform to their respective properties, performance, and stability data, creating a digital twin of all steps from raw materials to finished products. This network can then be analyzed via MaterialsZone’s built-in visualization tools and predictive machine learning models can be used to forecast experimental results before going into the lab!
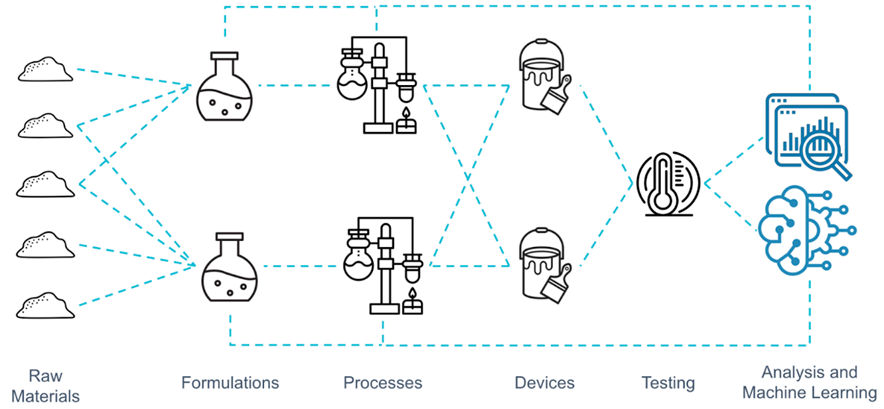
Visual Analyzer
The Visual Analyzer allows researchers to conduct multi-dimensional cross-correlation analysis, enabling them to intelligently design the materials composition based on desired product specifications.
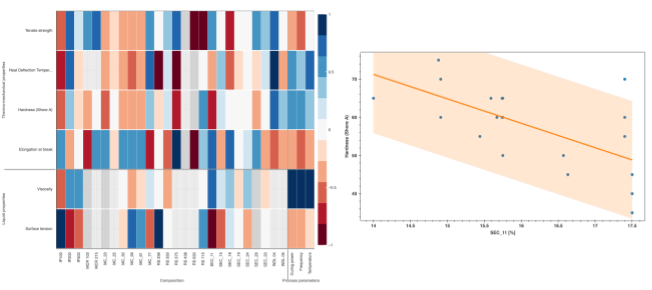
Predictive Co-Pilot
The Predictive Co-Pilot is able to recommend optimized formulations based on product requirements, whether they are desired material properties or external factors such as price or total process duration. This can help teams to easily navigate inter-dependent multidimensional problem spaces while balancing multiple, at times contradictory, product requirements. For example, the system can help researchers perform far fewer experiments in order to achieve the simultaneous optimization of a formulation’s whiteness (L*), gloss, and hiding power while considering the economic and environmental attributes of the raw materials.
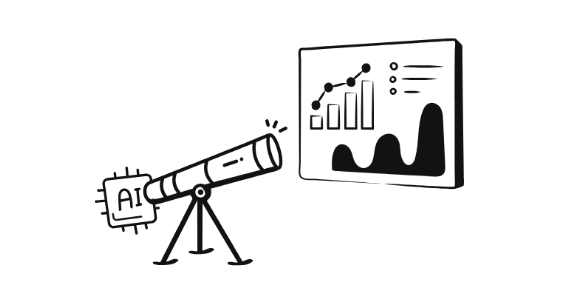
Reformulation and product development projects are being completed 50% faster, enabling teams to devote more time to analysis, process streamlining, and discoveries.