Parallel Process and Formulation Optimization in Additive Manufacturing

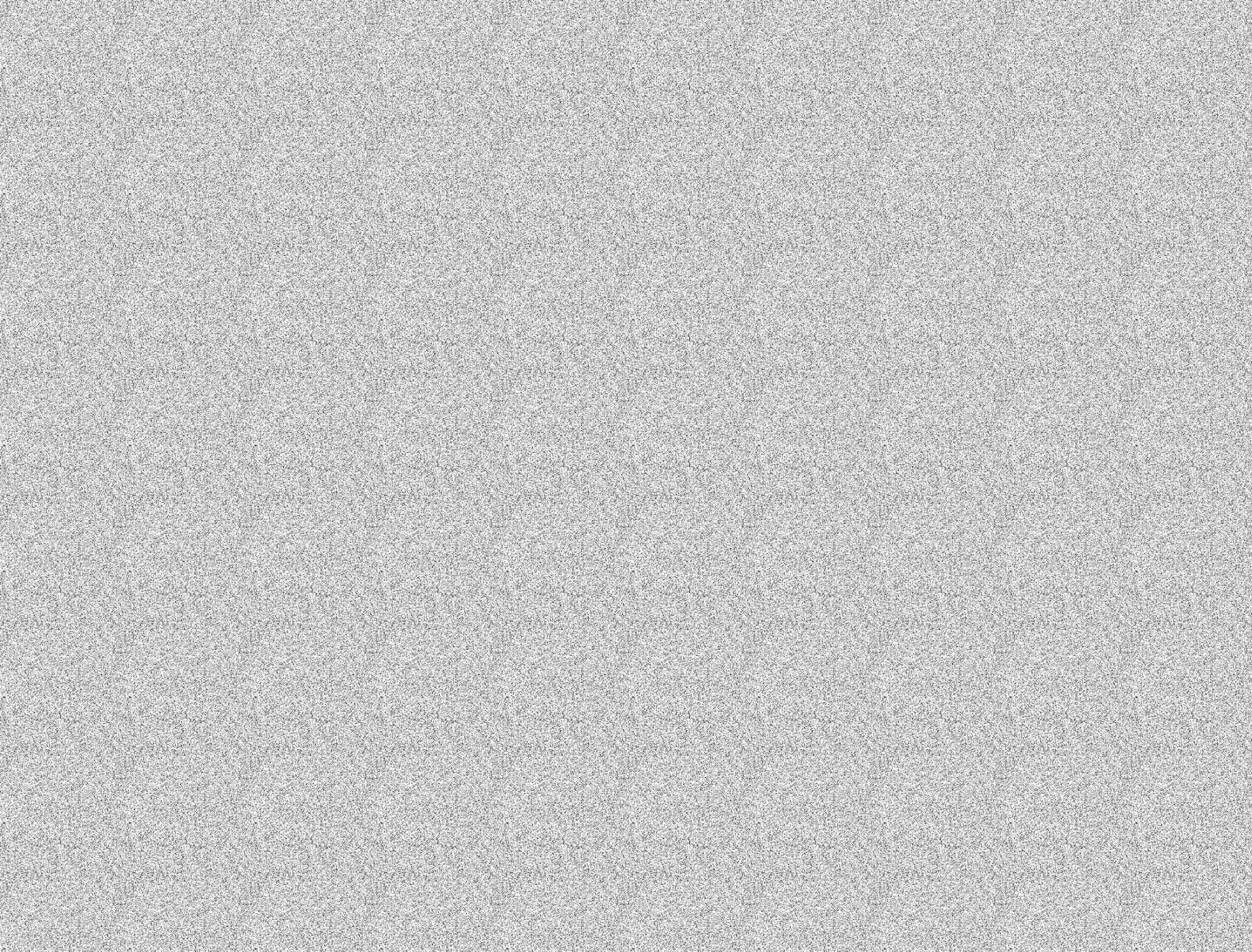
Additive manufacturing (AM) faces challenges due to the vast number of material formulations and process conditions, coupled with high costs and time for experiments. These challenges are further complicated by the need to optimize multiple, often conflicting material properties. The MaterialsZone platform addresses these challenges by combining efficient documentation and advanced Machine Learning (ML), enabling faster and more effective exploration and optimization. This approach has reduced experimental iterations by over 70% compared to traditional methods.
Problem
R&D in additive manufacturing involves exploring nearly infinite combinations of material formulations and process parameters, making optimization difficult, costly, and time-consuming. The complexity is increased by the need to balance multiple material properties, like strength, flexibility, and thermal stability, which may require conflicting optimization strategies. This makes it hard for research teams and managers to meet deadlines and find the best process and material combinations.
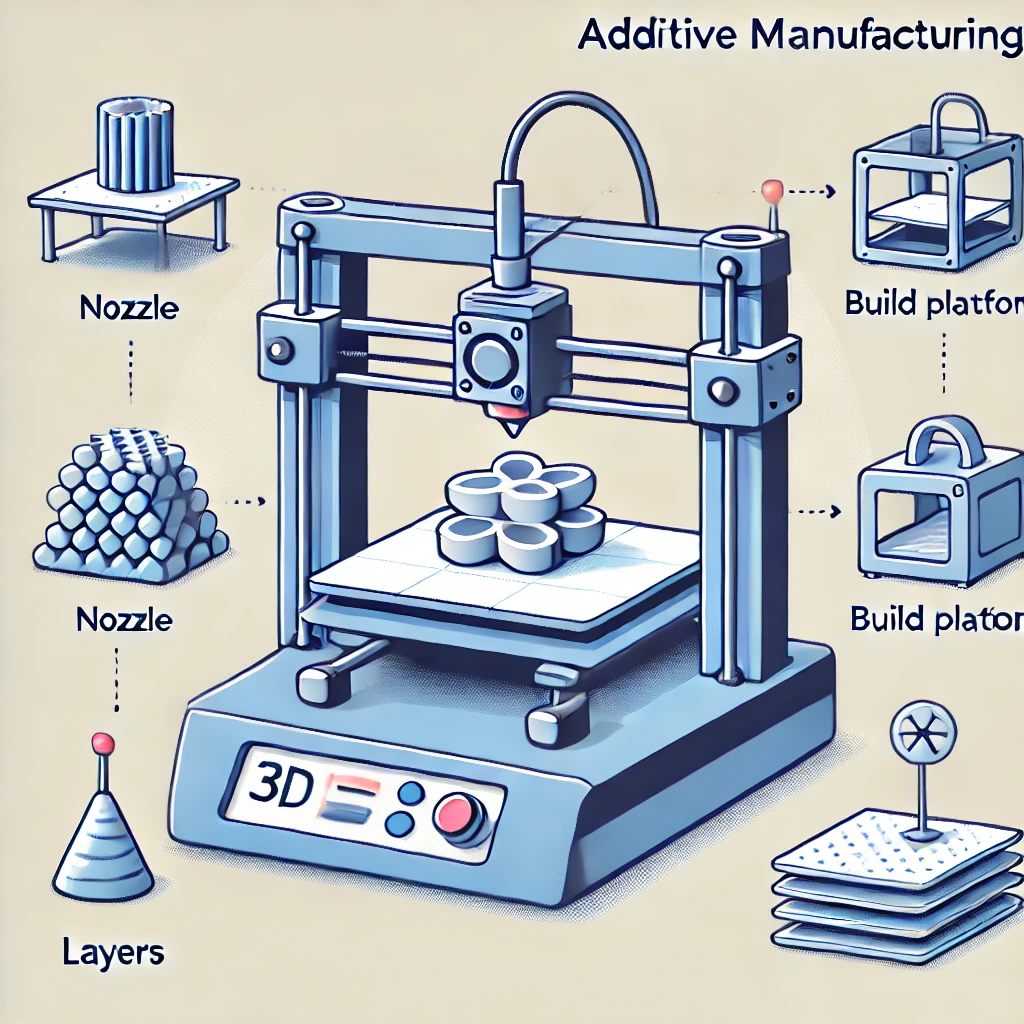
Solution
MaterialsZone's platform helps overcome these challenges in additive manufacturing by enabling parallel optimization of processes and material formulations. This is achieved through efficient experiment documentation and advanced Machine Learning techniques.
Efficient Experiment Documentation
To optimize material properties in AM, researchers must understand the cause-effect relationships between process parameters (like temperature and layer thickness) and material properties (like tensile strength and surface finish). MaterialsZone provides a centralized repository to document experiments in a standardized, machine-learning-ready format, making it easier to reference and reuse data. This promotes collaboration and streamlines the optimization process.
Predictive Co-Pilot for Experimental Design
The Predictive Co-Pilot on MaterialsZone helps researchers define their problem space, constraints, and targets. By using historical data, it leverages Machine Learning to suggest new experiments, either to explore the parameter space further or to optimize using existing knowledge. This "Active Learning Cycle" enriches data, trains models, and guides new experiments, accelerating development.
Active Learning Cycle in Additive Manufacturing
The Active Learning Cycle can start with little or no data, helping teams achieve optimal results with far fewer experiments than traditional methods. This is especially useful in AM, where rapid optimization of materials and processes is crucial for reducing time to market and ensuring high quality.
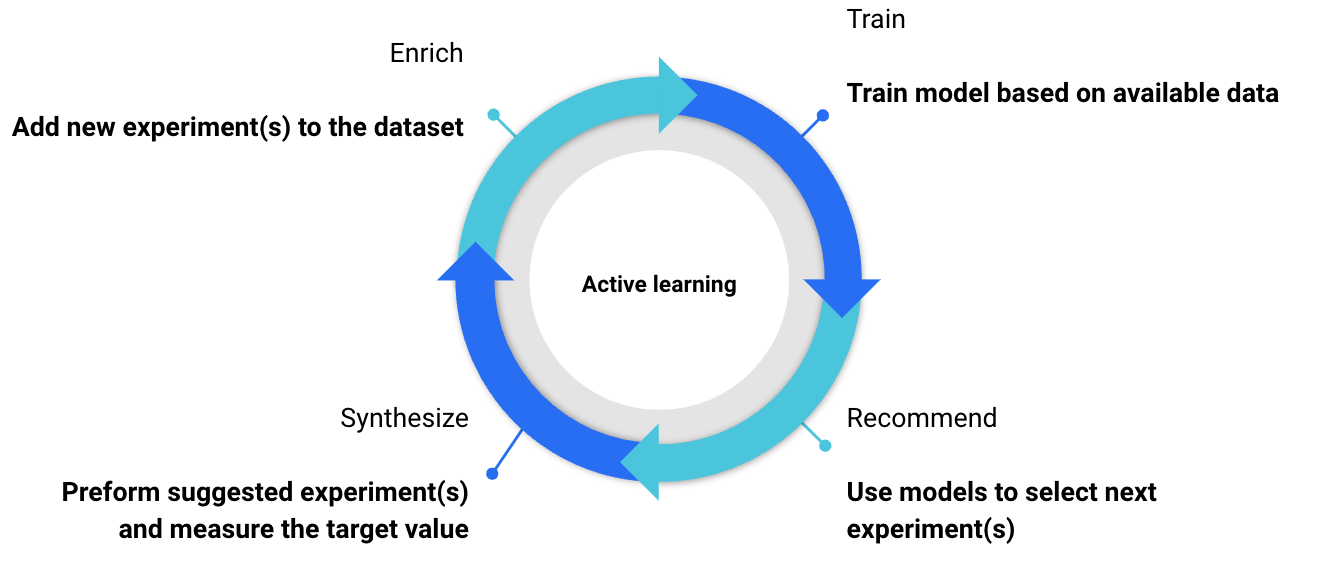
Outcome
By applying parallel optimization techniques, additive manufacturing teams can reduce experimental iterations by over 70%, speeding up development and cutting costs.
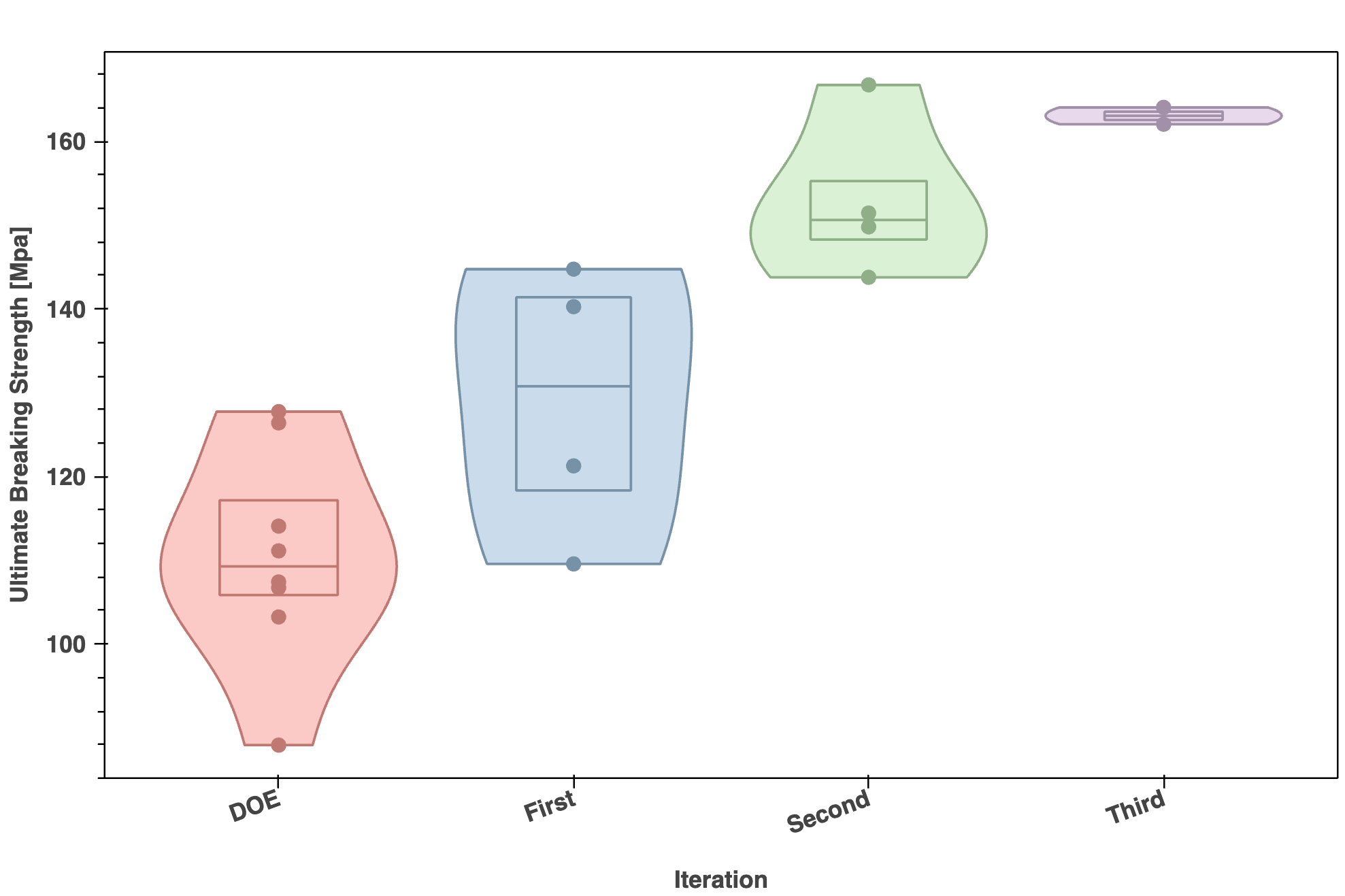