Top 10 Six Sigma Tools
Sometimes, small things have major consequences: A failed drug batch or a structural flaw in an advanced material can often be traced back to a seemingly minor deviation in the production process, like a slight shift in formulation or an overlooked equipment calibration.
.jpg)
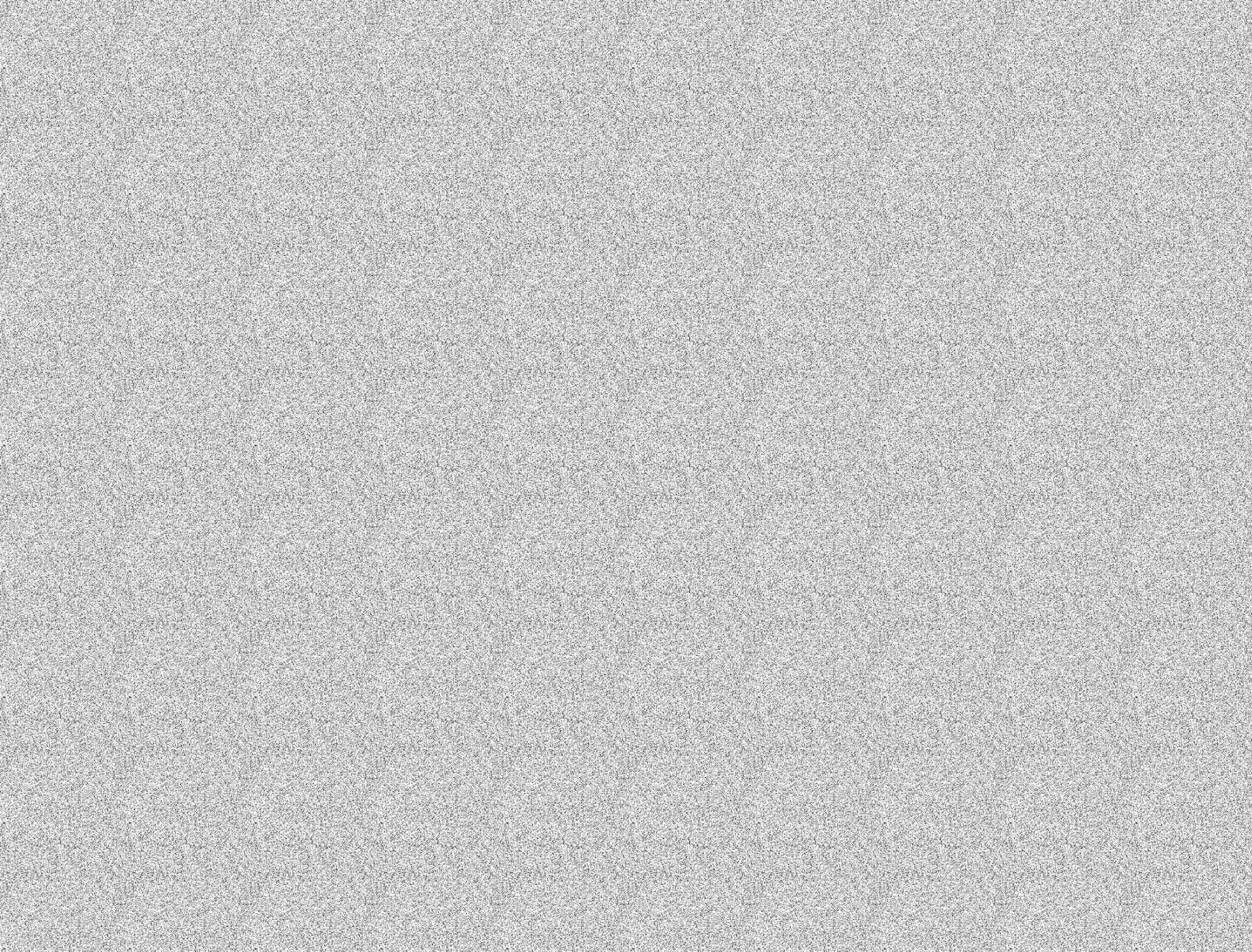
The results? Costly inefficiencies, regulatory violations, and lost revenue. The cost of poor quality in manufacturing can reach 15-20% of annual revenue as defects, rework, and inefficiencies quietly erode profitability. But identifying the root causes of defects and inefficiencies remains a challenge—even though companies in highly regulated industries generate massive amounts of process data.
Many teams rely on trial and error to troubleshoot recurring problems, but they waste time and resources doing so. Fortunately, there's a better way. Six Sigma tools provide a structured framework for reducing variability, improving efficiency, and ensuring that production processes remain controlled and repeatable. The 82% of Fortune 100 companies embracing these tools would undoubtedly agree.
When applied effectively, Six Sigma tools are essential for industries managing complex workflows and strict compliance requirements. Let's explore the Six Sigma methodology and the top ten tools to improve your approach to process improvement.
What Are Six Sigma Tools, and Why Do You Need Them?
Six Sigma is a structured methodology for improving process efficiency and quality by reducing defects and variability.
It provides organizations with a data-driven framework to identify inefficiencies, minimize waste, and create more reliable workflows. While initially developed for manufacturing, its applications now extend to industries that demand precision and compliance, such as materials science, chemicals, pharmaceuticals, and food production.

To achieve these improvements, Six Sigma relies on a specialized set of analytical techniques and problem-solving frameworks that help teams:
- Analyze process performance to detect inconsistencies.
- Identify root causes of defects using statistical methods.
- Implement corrective actions to ensure repeatability and compliance.
In industries where batch-to-batch consistency, measurement accuracy, and process validation are critical, these tools provide a structured way to control variability and maintain quality standards. Applying the right Six Sigma tools ensures that processes remain stable, predictable, and optimized for long-term success.
Who Benefits from Six Sigma Tools?
Six Sigma tools provide valuable benefits to R&D leaders, QA/QC managers, and production heads in many industries, including:
Pharma & Bio
Drug manufacturing depends on consistency and regulatory compliance. Six Sigma tools help standardize production, reduce batch variability, and meet FDA and EMA requirements. Statistical Process Control (SPC) monitors real-time variations in factors like temperature and humidity to detect deviations before they impact product quality. Failure Mode and Effects Analysis (FMEA) identifies risks before they impact quality.Food & BeverageQuality control ensures food safety and consumer trust. Six Sigma reduces variability to keep food and beverage products within strict standards. Process Mapping eliminates bottlenecks, and Pareto Analysis prioritizes issues affecting shelf life or contamination risks.

Chemicals
Precise control of chemical processes improves efficiency and reduces costs. Design of Experiments (DOE) optimizes chemical reaction conditions for higher yields, while Capability Analysis ensures key properties like pH and concentration remain within specifications.
Advanced Materials
High-performance materials require precision and reproducibility. DMAIC improves R&D workflows by identifying inefficiencies in experimental design and optimizing process steps, while Measurement System Analysis ensures testing instruments provide reliable results.
How Six Sigma Tools Enhance Materials Informatics
Materials informatics leverages AI and data analytics to accelerate material discovery and development. Six Sigma tools like Design of Experiments (DOE) and Statistical Process Control (SPC) bring structured methodologies to this process. It helps R&D teams:
- Identify patterns in complex datasets by analyzing experimental and simulated data to uncover trends in material behavior.
- Optimize material properties such as thermal stability, strength, and conductivity for applications in aerospace, electronics, and other advanced industries.
- Reduce development time by eliminating inefficiencies and improving decision-making throughout the research lifecycle.
MaterialsZone enhances these capabilities by integrating complex datasets, automating workflows, and delivering real-time, actionable insights. Its AI-driven analytics provide teams with a deeper understanding of material performance—enabling faster, more precise decision-making. By bridging Six Sigma methodologies with materials informatics, MaterialsZone helps organizations achieve greater efficiency and innovation.

Top 10 Six Sigma Tools for Optimizing R&D and Production
The top Six Sigma tools help analyze data, control processes, and improve efficiency. While all of these tools can be implemented manually, software is commonly used to speed up calculations, data visualization, and decision-making.
1. DMAIC (Define, Measure, Analyze, Improve, Control)
DMAIC is the foundational framework of Six Sigma for guiding structured process improvements. It's used for identifying inefficiencies, eliminating defects, and ensuring processes remain stable over time.
How it works:
- Define the problem and set objectives.
- Measure key performance indicators.
- Analyze data to find root causes of defects.
- Improve the process by implementing solutions.
- Control outcomes to prevent recurrence.
- DMAIC often integrates other Six Sigma statistical tools like SPC, Root Cause Analysis, and FMEA at various stages to enable data-driven decision-making throughout the process.
Use case: In pharmaceutical manufacturing, DMAIC helps improve tablet formulation consistency by identifying causes of batch variability and optimizing ingredient ratios for uniformity.
2. Design of Experiments (DOE)
DOE optimizes processes by understanding how different factors interact by employing a statistical approach to testing multiple variables simultaneously. Unlike one-factor-at-a-time (OFAT) testing, DOE determines cause-and-effect relationships in a structured way that makes it far more efficient.
How it works: DOE systematically varies input parameters to identify which combinations produce the best outcomes, which reduces trial-and-error experimentation.
Use case: In chemical manufacturing, DOE helps determine the ideal temperature, pressure, and catalyst concentrations to maximize reaction yield while minimizing waste.
3. Process Mapping (Flowcharts, Value Stream Mapping)
Visually representing workflows helps teams identify inefficiencies, redundancies, and opportunities for improvement. Flowcharts and Value Stream Mapping (VSM) optimize process flow by eliminating unnecessary steps, reducing delays, and improving resource allocation.
How it works:
- Flowcharts are step-by-step diagrams that outline a process using standardized symbols (e.g., rectangles for tasks, diamonds for decision points). Flowcharts help teams visualize a workflow from start to finish, which makes it easier to spot inefficiencies such as duplicated efforts or unclear handoffs.

- Value Stream Mapping (VSM) is a Lean Six Sigma technique that provides a high-level overview of how materials and information move through a process. Unlike basic flowcharts, VSM includes data on cycle times, delays, and inventory levels. They help teams quantify inefficiencies and focus on high-impact improvements.

Use case: In advanced materials R&D, process mapping helps streamline data collection from multiple labs. A flowchart can map data as it moves from experimental testing to final analysis, identifying bottlenecks in approvals. A VSM would provide deeper insights into where delays occur, such as extended wait times for lab results or inefficient handoffs between research teams.
4. Failure Mode and Effects Analysis (FMEA)
FMEA is a proactive risk assessment tool that identifies potential failure points and their impact. It helps prevent defects by prioritizing high-risk areas in a process.
How it works:
- Teams assign risk scores based on severity, occurrence likelihood, and detectability.
- Using these scores, a Risk Priority Number (RPN) is calculated to determine which issues require immediate attention.
Use case: In biotechnology, FMEA helps prevent contamination risks in sterile drug production by evaluating weak points in cleanroom protocols and prioritizing fixes based on risk severity.
5. Control Charts
Control Charts are visual tools that track process performance over time. They’re important because the data they provide is critical in maintaining process stability and detecting deviations early.
How it works:
- Data points are plotted against upper and lower control limits.
- Trends are analyzed to identify potential quality issues.
- Control charts are often used with Capability Analysis (Cp, Cpk) to ensure that processes remain stable and also meet quality specifications.
Use case: In semiconductor manufacturing, control charts track wafer thickness consistency to ensure microchips are reliable and meet design tolerances.
6. Root Cause Analysis (5 Whys, Fishbone Diagram)
Root Cause Analysis is really two tools in one. The 5 Whys and Fishbone Diagram are structured problem-solving techniques used to identify the fundamental cause of defects or inefficiencies. Together, they prevent recurring issues by addressing the root cause rather than treating surface-level symptoms.How it works:
- 5 Whys - This method involves repeatedly asking "why" to drill down into the true cause of a problem. For example, if a batch of advanced materials fails stress testing, asking "why" five times might uncover that improper curing conditions—not just material composition—caused the defect.
- Fishbone Diagram (Ishikawa Diagram) - This visual tool categorizes possible causes of a problem into key areas such as equipment, materials, process, environment, and personnel. It is especially useful when a problem has multiple contributing factors beyond what the 5 Whys alone can uncover.
Use case: In materials science, Root Cause Analysis helps identify why a composite material is failing under stress. The 5 Whys might reveal that improper fiber orientation is the issue, while a Fishbone Diagram would categorize contributing factors such as equipment settings, environmental humidity, and resin formulation inconsistencies.

7. Capability Analysis
A statistical method for determining whether a process consistently meets specifications, Capability Analysis is used for evaluating process reliability and compliance with industry standards.
How it works:
- Capability indices (Cp, Cpk) compare process variation against tolerance limits to assess performance.
- While Cp measures capability assuming centering, Cpk accounts for shifts, making it a more accurate indicator of process performance.
Use case: In pharmaceuticals, capability analysis ensures tablet dissolution rates remain within therapeutic efficacy limits for drug effectiveness.
8. Statistical Process Control (SPC)
SPC is a real-time process monitoring method that uses statistical techniques to detect variations in production before defects occur.
How it works: SPC charts real-time process data against control limits to identify deviations that require intervention. This reduces waste and ensures compliance.
Use case: In food production, SPC ensures pasteurization temperatures remain within FDA-specified limits to help prevent bacterial contamination.
9. Measurement System Analysis & Gage R&R
These two statistical methods evaluate the reliability of a measurement system by determining how much variation comes from the measuring process itself rather than the product being measured. They ensure measurement systems are accurate, consistent, and repeatable.How it works:
- MSA evaluates all sources of variation, including equipment, operator technique, and environmental conditions.
- Gage R&R quantifies variation due to repeatability, reproducibility, and equipment inconsistencies.
- Other MSA techniques employed include stability, linearity, and bias analysis. They assess accuracy over time and across measurement ranges.
Use case: In pharmaceutical quality control, MSA and Gage R&R validate spectrophotometer accuracy for drug composition testing.

10. Pareto Analysis (80/20 Rule)
Focusing your efforts on the most impactful issues is the key to efficient processes. Pareto Analysis is a prioritization tool based on the principle that 80% of problems come from 20% of causes.
How it works: Teams analyze defect data to determine which factors contribute the most to inefficiencies, then allocate resources accordingly.
Use case: In chemical processing, Pareto analysis helps identify which equipment failures are responsible for the majority of downtime to better guide preventive maintenance.
Stronger Processes, Smarter Decisions: Six Sigma Tools & MaterialsZone
Implementing Six Sigma in R&D, production, and quality control requires a systematic, data-driven approach. Leveraging these Six Sigma tools allows organizations to reduce variability, improve efficiency, and maintain compliance. The true strength of Six Sigma lies in integrating multiple tools to drive lasting process improvements.MaterialsZone's AI-driven platform strengthens Six Sigma implementation by automating data collection, ensuring compliance, and improving measurement accuracy. With real-time insights and predictive analytics, teams can create stronger processes and make smarter decisions that help them get innovative products to market faster than ever.
Request a demo today to see how MaterialsZone transforms Six Sigma tools into action.