The Essential Guide to the 13 Mechanical Properties of Metal
Selecting the right metal for R&D and manufacturing is more complex than ever. Choosing the wrong material can cause costly delays, failed prototypes, and compromised product performance. In industries where precision is crucial—such as aerospace, pharmaceuticals, and advanced materials—understanding a metal's mechanical properties is fundamental to ensuring durability, compliance, and reliability.
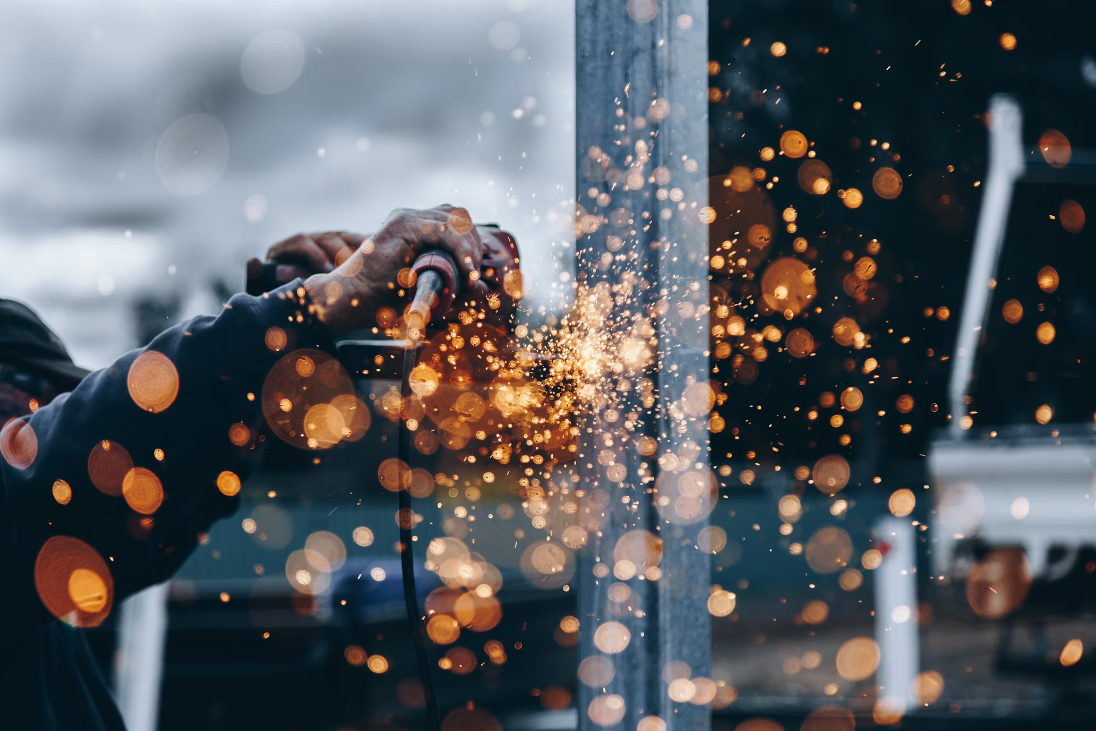
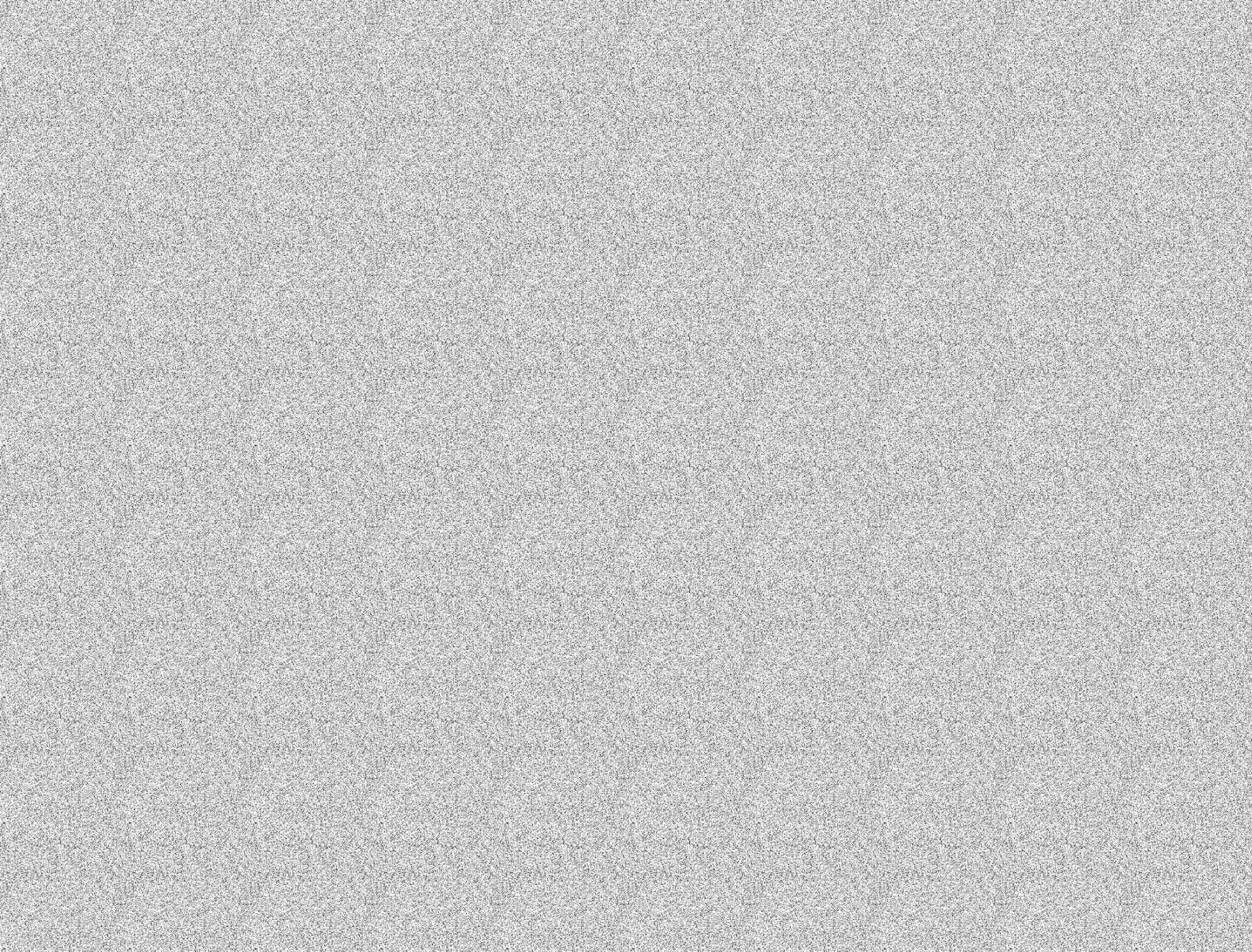
Recent studies show that 51% of errors in metal fabrication are caused by picking the wrong materials. This statistic highlights how overlooking the mechanical properties of metal can lead to product failures, recalls, and regulatory issues. As materials become more specialized and regulations more stringent, R&D teams must adopt a data-driven approach to material selection.
This guide explores 13 essential mechanical properties of metal, how they impact material performance, and how leveraging material informatics can optimize R&D and manufacturing decisions.
What Are Mechanical Properties of Metal, and Why Are They Important to R&D?
Mechanical properties describe how metals respond to external forces such as tension, compression, impact, and heat. These properties define whether a material can withstand stress, maintain its structure, and perform reliably under real-world conditions.
Understanding the metals' mechanical properties is essential for R&D teams to make informed decisions that improve material selection and product design.
Ensuring Performance, Compliance, and Innovation
Mechanical properties must be accurately measured to ensure materials meet performance, safety, and compliance requirements (including GLPs). Engineers and scientists use standardized testing methods to evaluate these properties, including:
- Tensile Testing – Measures how much force a metal can withstand before breaking under tension, ensuring its suitability for load-bearing applications.
- Impact Testing – Assesses a material's ability to resist sudden forces by measuring the energy it absorbs upon impact, which is critical in crash protection and safety applications.
- Fatigue Testing – Determines a metal's endurance under repeated stress cycles, helping predict material lifespan in components like aircraft wings and rotating machinery.
- Hardness Testing – Evaluates resistance to indentation and wear using methods like Rockwell, Brinell, and Vickers hardness tests.
These tests provide essential data that informs material selection, design, and performance optimization in industrial applications.
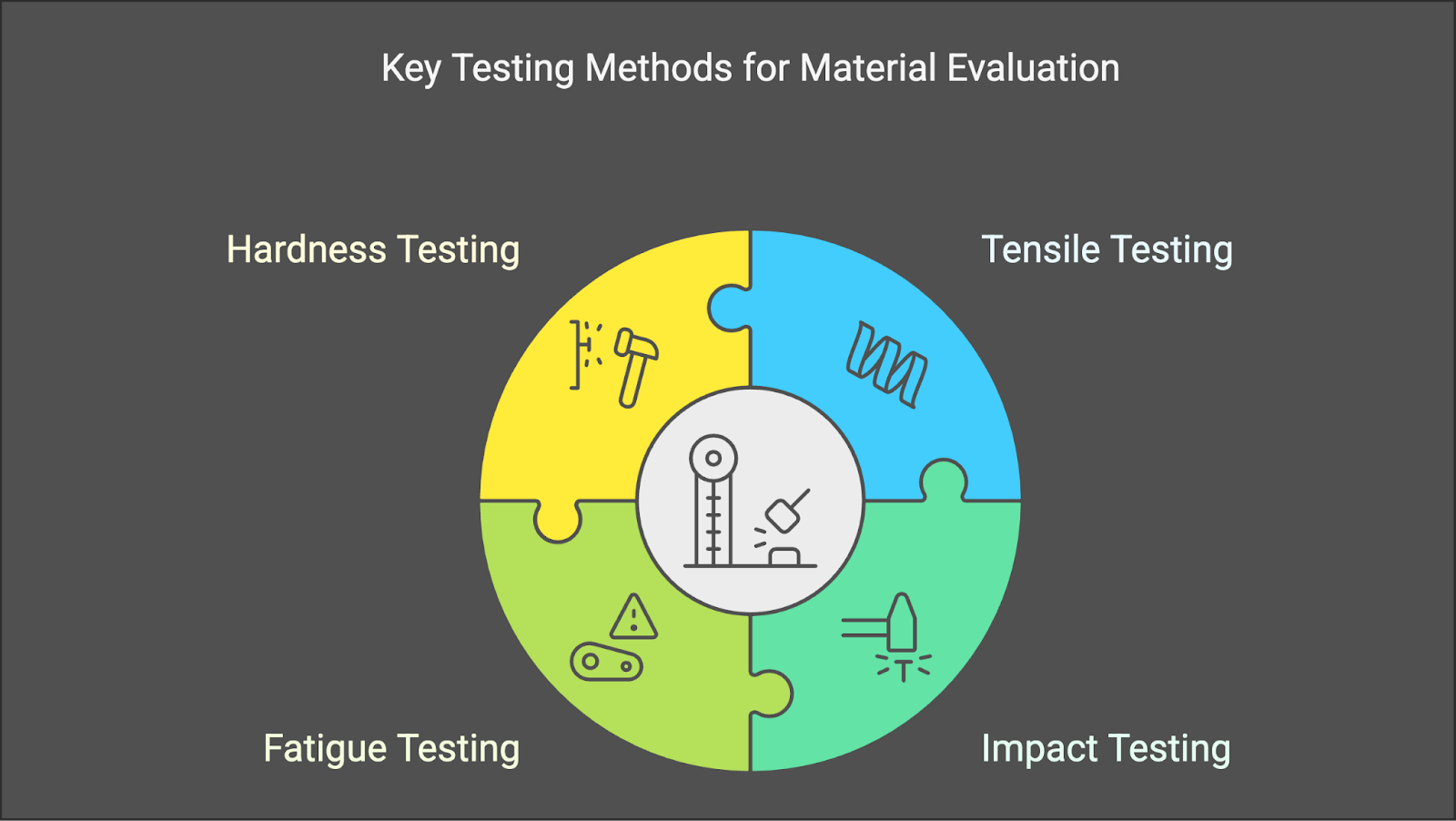
The Role of Mechanical Properties in Material Performance
In R&D, mechanical properties determine a metal's suitability for specific applications. Selecting the wrong material can lead to product failures, costly redesigns, and regulatory setbacks. For example:
- In aerospace, an error in fatigue strength calculations can result in catastrophic structural failure.
- In pharmaceutical manufacturing, improper hardness can lead to contamination in drug production.
- In automotive engineering, poor impact resistance can increase the risk of material failure during crashes.
Companies that embrace product-led growth (PLG) use data-driven material selection to enhance product performance and increase reliability while reducing time-to-market—but you can also get similar results with material informatics.
How Material Informatics Helps Mechanical Property Analysis
Material informatics is transforming how mechanical property data is analyzed by integrating multi-source datasets and predictive modeling. This allows R&D teams to:
- Correlate mechanical properties with real-world performance to optimize material selection.
- Leverage AI-driven insights to predict how different metals will behave under specific conditions.
- Streamline compliance by integrating mechanical test data with regulatory requirements.
Platforms like MaterialsZone provide tools that enable researchers to evaluate and compare mechanical properties more effectively, reducing costs, improving efficiency, and accelerating innovation. Leveraging the data-driven decision-making provided by materials informatics solutions allows R&D teams to make more precise material choices that ensure durability, safety, and performance in real-world applications.
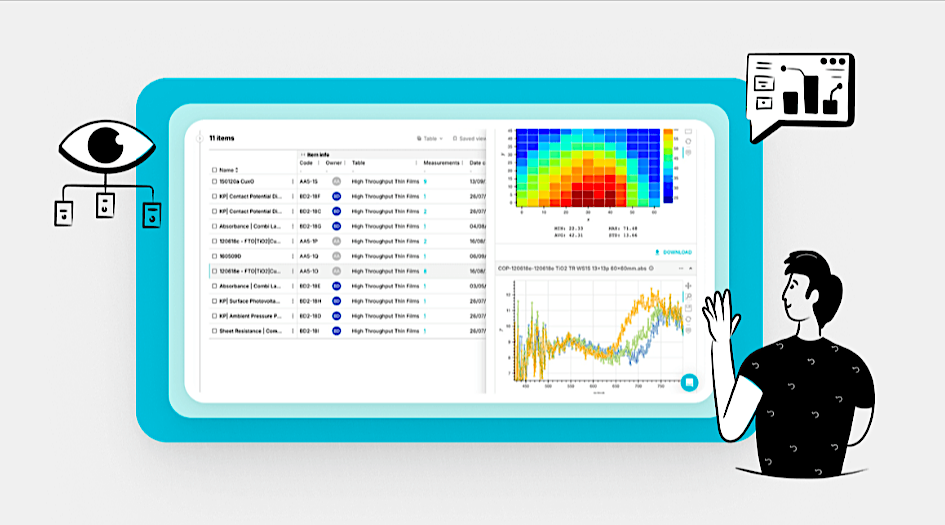
13 Key Mechanical Properties of Metal
Here are the fundamental mechanical properties of metal and how they influence material selection and product performance:
Fundamental Forces
1. Tensile Strength
Tensile strength describes the maximum stress a material can endure before breaking under tension. It is a crucial property for materials used in high-stress environments to ensure they do not fail under pulling forces.
In R&D, understanding tensile strength allows engineers to select metals that can withstand operational forces in applications such as bridges, aircraft fuselages, and structural cables. This property is typically measured through tensile testing, where a sample is stretched until failure.
2. Compressive Strength
Compressive strength measures a material's ability to resist deformation when subjected to compressive forces. It is vital for applications where materials must withstand high-pressure loads without buckling or breaking.
Metals with high compressive strength, such as steel and titanium, are essential in structural engineering, construction, and industrial manufacturing. Standardized compression tests help engineers determine a material's ability to withstand applied pressure, which is crucial for maintaining stability in load-bearing applications.
3. Shear Strength
Shear strength determines a metal's resistance to forces that cause layers within the material to slide past each other. This property is critical in mechanical joints, fasteners, and welded components that experience lateral stresses.
In industries such as automotive and aerospace, high shear strength is essential for the durability of rivets, bolts, and load-bearing structures. Engineers evaluate this property using shear tests that apply force parallel to the material's surface until failure occurs.
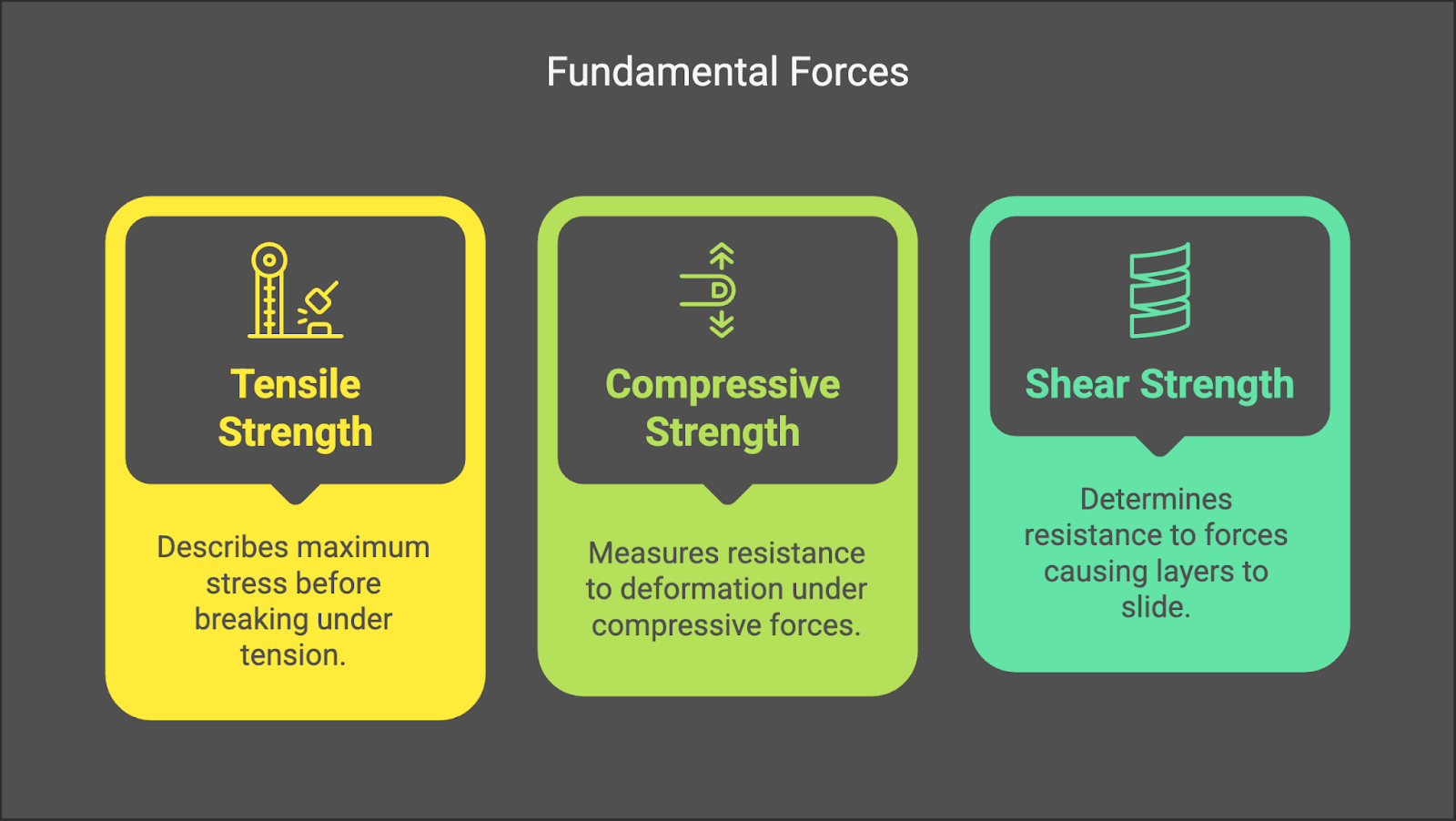
Elastic Behavior
4. Young’s Modulus
Young's modulus quantifies a material's stiffness, specifically its resistance to elastic deformation. It measures how much a material deforms elastically (reversibly) under a given stress. While Young's modulus is applicable in other ways to a variety of materials, it’s most commonly used for metals in the mechanical property context.
In R&D, Young's modulus is fundamental in material selection for structural applications, allowing engineers to predict how materials will behave under load. Because it quantifies stiffness, it directly relates to how much a structure deflects under load. Practical applications include determining the deflection of bridges and buildings, ensuring stability in load-bearing structures, and designing components where stiffness is critical.
Young's modulus is determined by a tensile test, wherein a material sample is subjected to a controlled tensile force, and the resulting elongation is measured. A higher value of Young's modulus signifies that the material exhibits greater stiffness, meaning it is more resistant to deformation under applied stress.
5. Elasticity
Elasticity is the property of a material that allows it to return to its original shape after deformation when the applied stress is removed. It's the behavior that Young's modulus quantifies. All materials exhibit some degree of elasticity, including metals.
Understanding elasticity (and how it's quantified by Young's modulus) is crucial in R&D for designing metal components that require flexibility and resilience. Practical applications include springs, flexible couplings, and shock absorbers.
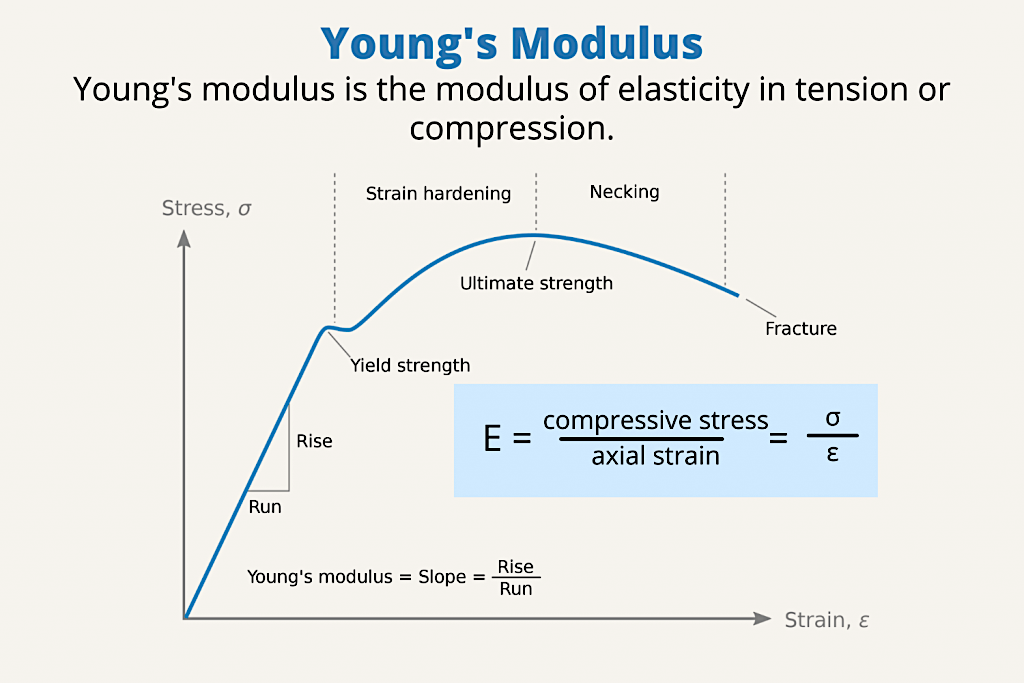
Deformation Properties
6. Plasticity
Plasticity refers to a metal's ability to undergo permanent deformation without breaking. It is a key property in shaping and forming processes, allowing metals to be molded into desired shapes without cracking.
High-plasticity metals like aluminum and copper are widely used in forging, extrusion, and rolling processes. Engineers assess plasticity through stress-strain testing to determine how much a material can be deformed before failure.
7. Ductility
Ductility measures a material's ability to stretch into thin wires or sheets without breaking. It is a critical property in industries requiring metal reshaping, such as electrical wiring and aerospace fabrication.
Ductile metals like copper, gold, and aluminum allow manufacturers to create intricate designs without compromising material integrity. Engineers evaluate ductility by measuring a material's elongation percentage under tensile stress.
8. Brittleness
Brittleness is the tendency of a material to fracture rather than deform when subjected to stress. While brittle materials are not ideal for structural applications, they are useful in areas requiring hardness and wear resistance.
Cast iron and ceramics, for example, exhibit brittleness but are valuable in wear-resistant coatings and cutting tools. Engineers measure brittleness through impact tests to determine a material's ability to withstand sudden forces without breaking.
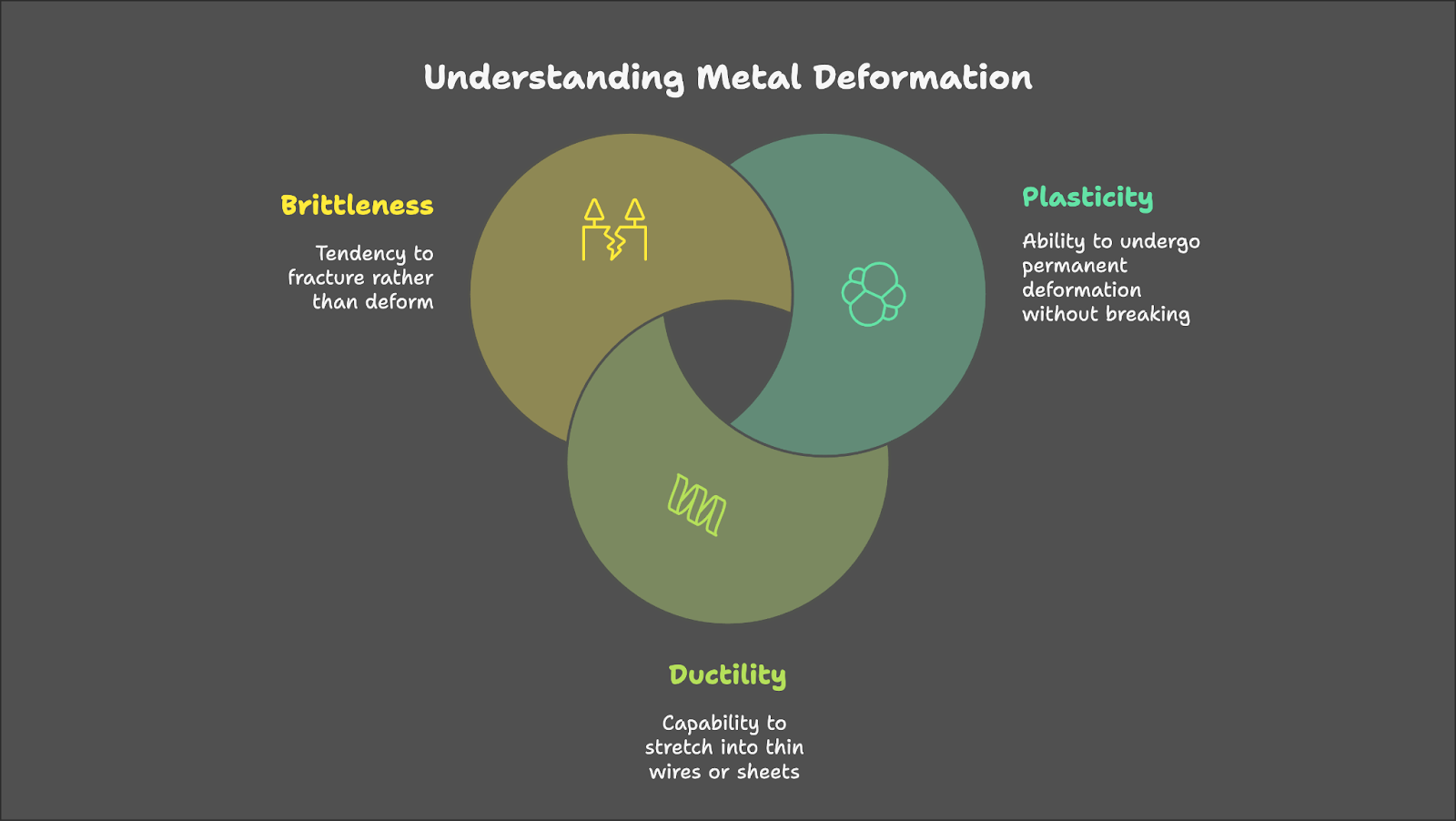
9. Impact Strength
Impact strength measures a metal's ability to resist sudden, forceful impacts without breaking. It is crucial in applications requiring high resilience. Safety gear, automotive frames, and protective barriers require metals with high impact resistance.
Engineers determine this mechanical property of metal through tests such as:
- Charpy Test – A pendulum hammer strikes a notched metal sample on the opposite side of the notch, and the energy absorbed during fracture is measured. This test evaluates a material's toughness and ability to withstand sudden impact forces.
- Izod Test – Similar to the Charpy test but differs in setup: the metal sample is clamped vertically, and the hammer strikes it on the same side as the notch. It's used to assess impact resistance in metals and polymers.
These tests provide critical insights into a material's ability to withstand sudden impact forces in real-world applications.
10. Toughness
Toughness represents a material's ability to absorb energy and resist fracture under sudden impact. Unlike hardness, which measures surface resistance, toughness evaluates how well a material withstands dynamic forces.
This property is crucial in construction, automotive safety, and aerospace industries, where materials must endure unpredictable stresses. The Charpy test and Izod test are commonly used to measure a material's toughness by evaluating how much energy it absorbs before fracturing under impact.
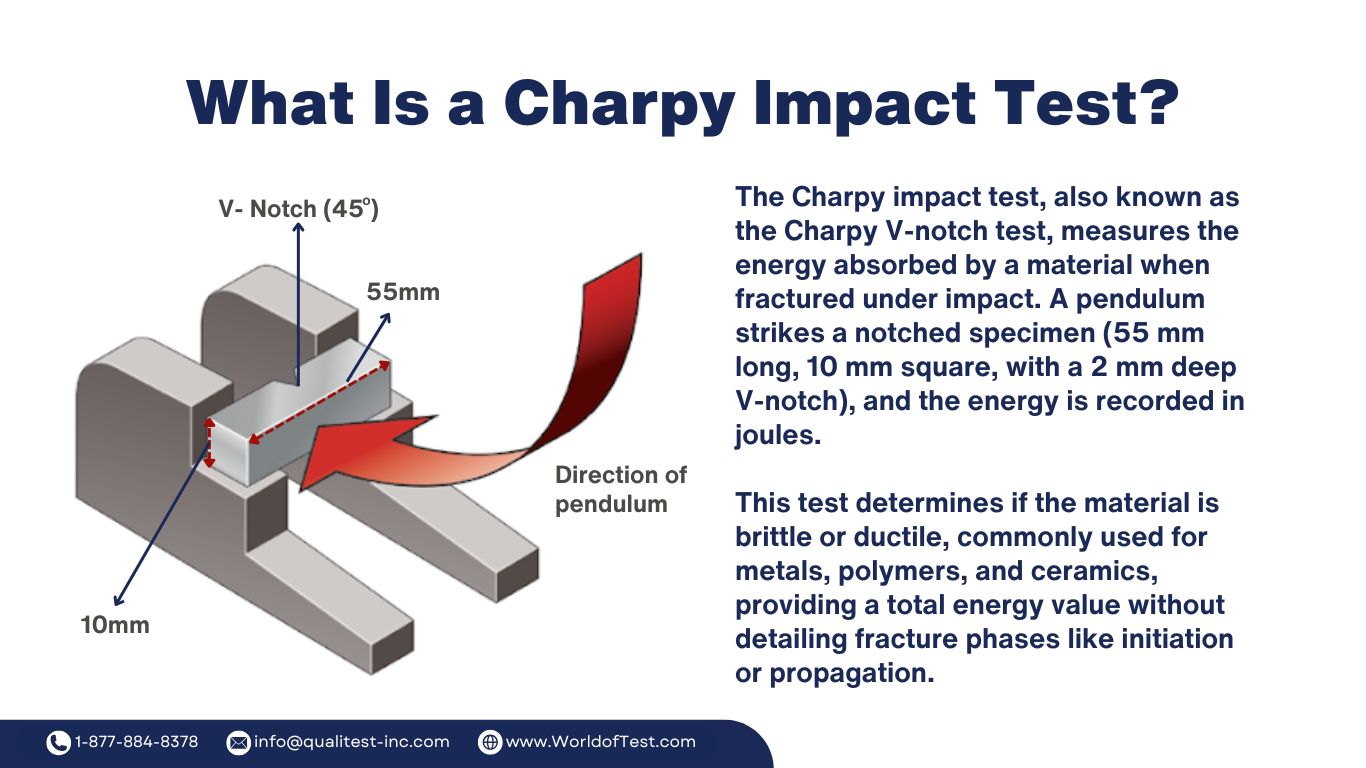
11. Hardness
Hardness determines a metal's resistance to indentation, scratching, and wear. This property is essential in applications where durability and surface protection are crucial.
High-hardness materials, such as tungsten carbide and hardened steel, are used in cutting tools, industrial machinery, and protective coatings.
Engineers assess hardness using tests like:
- Rockwell Test - A steel or tungsten carbide ball is pressed into the material while under a specific load, and the indentation depth is measured.
- Brinell Test - This test uses a larger steel ball and measures the diameter of the indentation left on the surface. These methods help determine a material's resistance to wear and deformation in industrial applications.
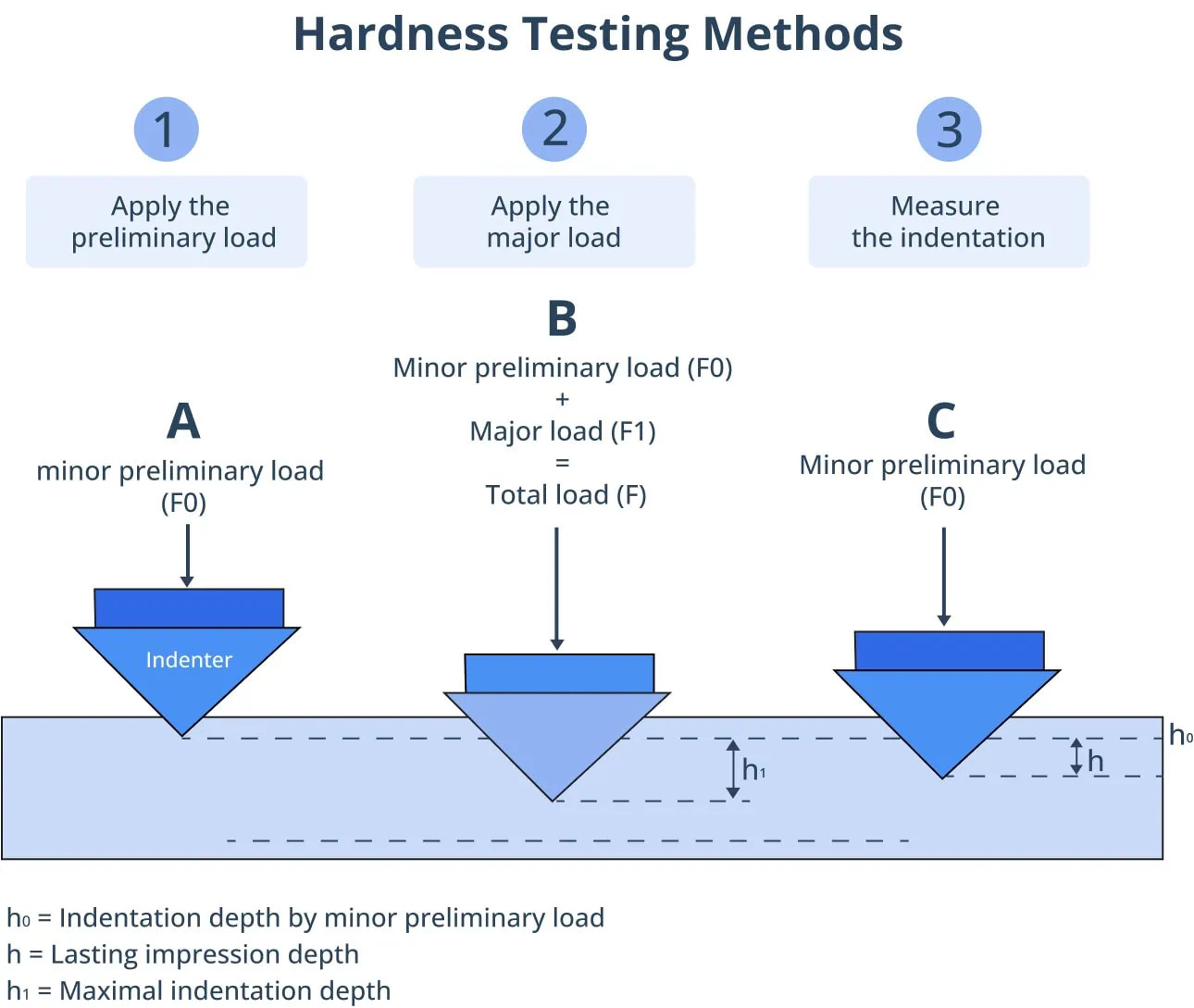
12. Fatigue Strength
Fatigue strength assesses a metal's ability to withstand repeated loading and unloading cycles without failure. It is a key property in components subjected to continuous stress.
Aircraft wings, bridges, rotating machinery, and warehouse robots rely on materials with high fatigue strength to prevent long-term degradation. In robotic arms and autonomous mobile robots (AMRs), components such as actuators and structural frames must endure constant motion and load cycles without failure.
Fatigue testing is conducted by subjecting a material to repeated loading and unloading cycles that simulate real-world conditions. This test helps predict how long a material can withstand cyclic stress before developing cracks or failing.
13. Creep Strength
Creep strength measures a material's resistance to slow deformation under prolonged stress and high temperatures. This property is vital in industries like aerospace and power generation.
Metals like nickel alloys are commonly used in jet engines and turbines, where materials must maintain integrity under extreme heat, often exceeding 900°C (1652°F). Engineers evaluate creep resistance through long-term stress testing to assess how materials deform over extended periods at elevated temperatures.
A commonly used standardized creep strength test method is ASTM E139, which was developed by the American Society for Testing and Materials (ASTM) to evaluate the creep and stress-rupture behavior of metals in these high-stakes environments.
Leverage MaterialsZone to Optimize Material Selection
Understanding the opportunities around the mechanical properties of metal is essential for R&D teams striving for material optimization, regulatory compliance, and product reliability. Choosing the right metal reduces failures and ensures durability in projects across industries. However, to achieve this, companies must move beyond traditional trial-and-error approaches.
MaterialsZone empowers R&D teams with data-driven material selection. It offers insights through material informatics, predictive analytics, and multi-source data integration. Leveraging these tools enables organizations to enhance performance, reduce costs, and get new products to market faster.
Explore MaterialsZone today to discover how data-driven insights help optimize material selection.