8 Steps to Optimize the Masterbatch Manufacturing Process
What if your manufacturing process didn't just meet demand but gave you a competitive advantage? The masterbatch manufacturing process is essential for producing high-performance materials with consistent quality, efficient production, and sustainability compliance. Optimizing this process allows manufacturers to unlock innovation and adapt to the growing demands of modern industries.
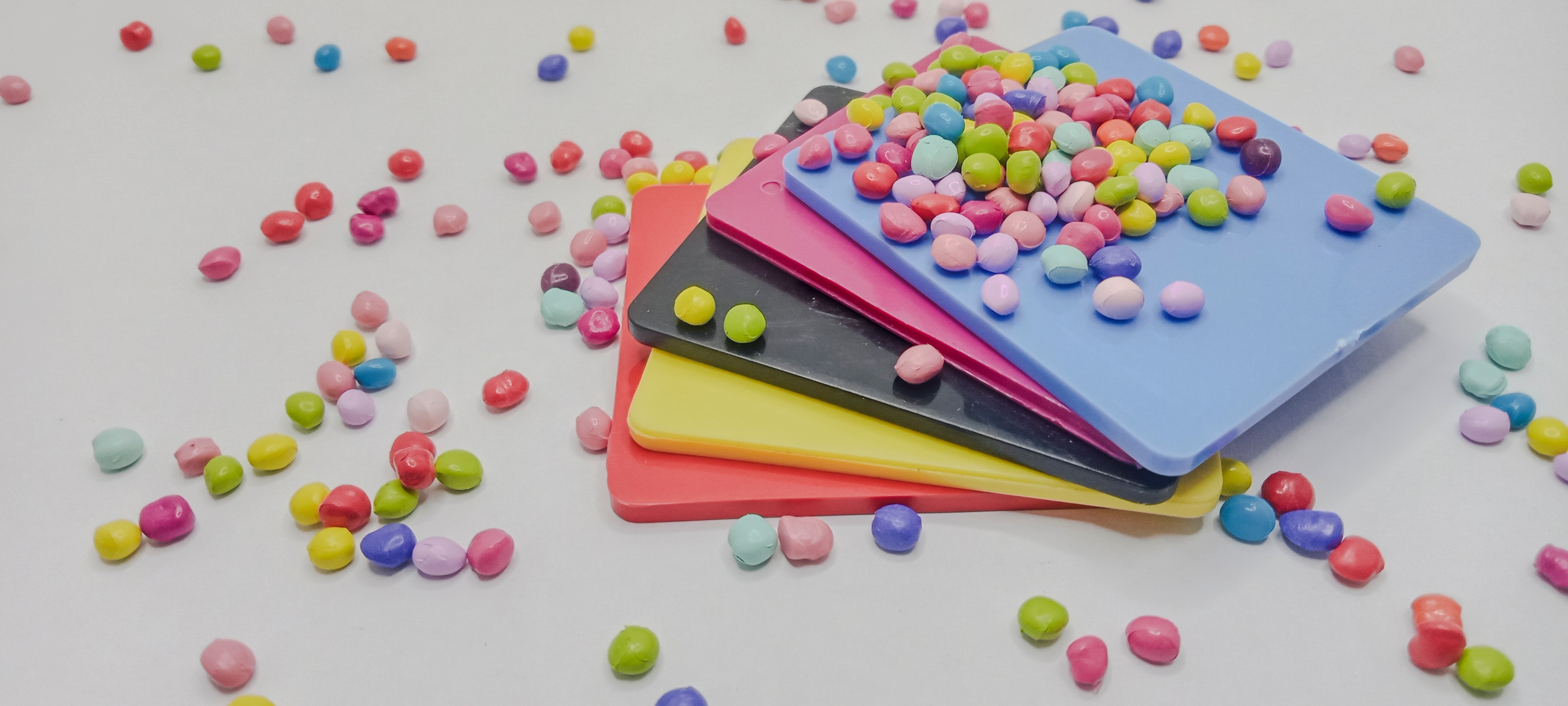
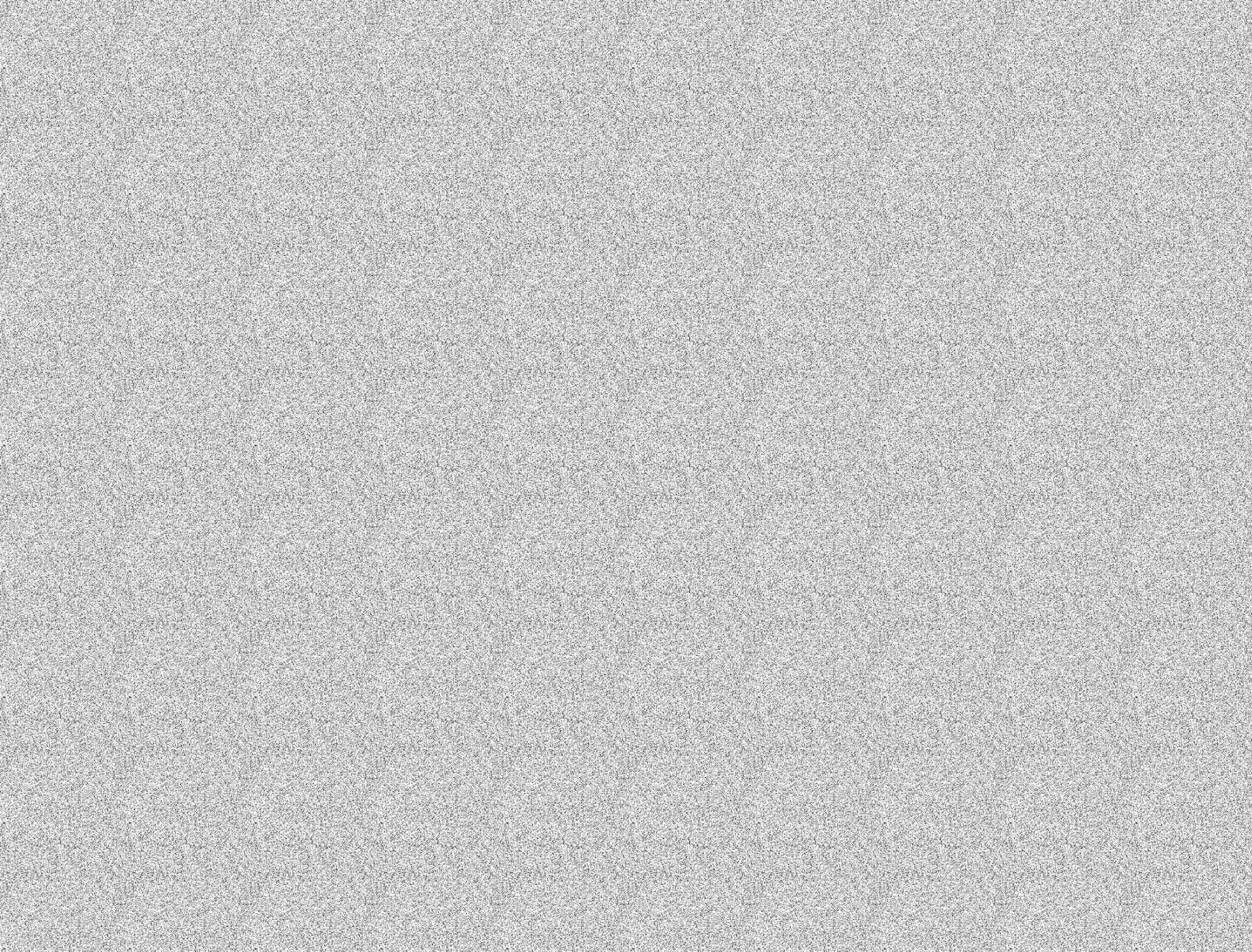
The global demand for masterbatches will grow to $19.58 billion by 2030. This growth reflects their increasing use in industries like automotive and packaging, where companies are replacing traditional materials with advanced plastics to improve performance and reduce environmental impact.
To stay competitive, manufacturers must move beyond traditional methods and embrace smarter strategies. By leveraging advanced techniques, data-driven insights, and streamlined workflows, the masterbatch manufacturing process can become a catalyst for innovation and success. Let's explore eight steps to help you optimize this critical process.
What Is the Masterbatch Manufacturing Process, and Why Is it Important?
The masterbatch manufacturing process is a method of producing a concentrated mixture of pigments and additives encapsulated in a carrier resin. This process simplifies handling and ensures seamless integration into plastics production, making it an essential step in manufacturing high-performance materials.
Encapsulating pigments and additives ensure uniform color, dependable performance, and consistent material properties in the final product. Achieving this level of consistency is crucial for meeting industry standards and maintaining quality across diverse applications.
Masterbatches are widely used in the packaging, automotive, construction, and consumer goods industries. They enhance product characteristics by adding functionality such as UV protection, flame retardancy, or vibrant colors. For example, packaging applications rely on masterbatches for durable, visually appealing designs, while the automotive sector uses them to create lightweight yet durable components.
In R&D and materials science, the masterbatch manufacturing process is a cornerstone of innovation. It accelerates prototyping, supports product customization, and ensures compliance with strict quality standards. These capabilities make it a pivotal process for driving advancements in product development.
Benefits of the Masterbatch Manufacturing Process
The masterbatch manufacturing process offers several advantages that make it indispensable for industries relying on high-performance materials:
Consistent Quality Across Batches
The process ensures uniform distribution of pigments and additives, delivering consistent color, performance, and material properties in the final product. This consistency is critical for meeting industry standards and preventing defects like streaking or uneven coloring.
Cost Efficiency
Consolidating pigments and additives into a single concentrate reduces material waste and streamlines production workflows. Manufacturers save on raw materials and operating costs, boosting overall profitability.
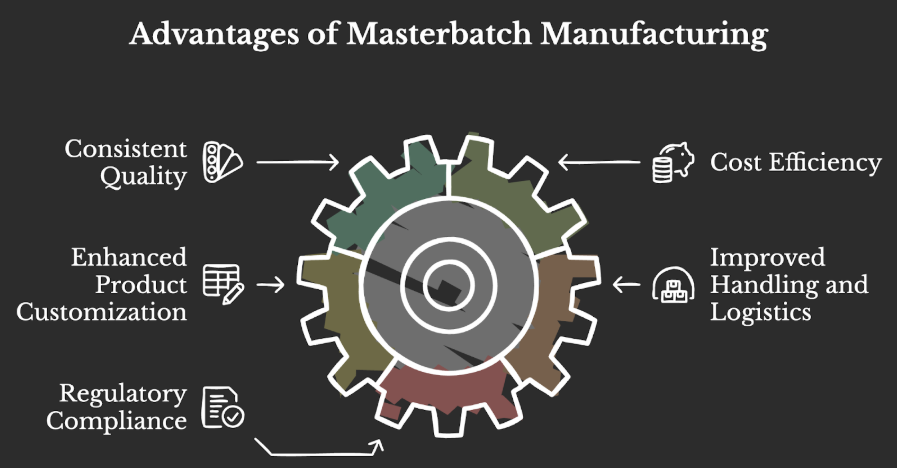
Enhanced Product Customization
Masterbatches allow manufacturers to tailor material properties to specific needs, such as UV resistance, flame retardancy, or unique colors. This flexibility supports innovation and meets the demands of specialized applications in diverse industries.
Improved Handling and Logistics
Encapsulated pigments and additives simplify storage, transportation, and mixing, making operations safer and more efficient. This reduces risks associated with handling raw materials and minimizes logistical complexities.
Regulatory Compliance
The masterbatch manufacturing process supports adherence to strict environmental and safety standards, such as REACH and RoHS. With thorough documentation and consistent formulations, manufacturers can bolster compliance and reduce the risk of penalties.
8 Steps to Optimize the Masterbatch Manufacturing Process
Optimizing the masterbatch manufacturing process is key to achieving consistent quality, cost efficiency, and regulatory compliance. Here are eight steps with actionable strategies that will help you streamline operations and outperform the competition:
Step 1: Raw Material Selection and Preparation
Selecting and preparing high-quality raw materials is the foundation of a successful masterbatch manufacturing process.
Carrier resins, pigments, and additives must be chosen carefully to ensure compatibility, performance, and efficiency. Proper preparation minimizes production waste, ensures consistency, and improves the overall quality of the final product.
Optimization Strategies:
- Evaluate carrier resins for thermal stability, chemical compatibility, and application-specific requirements.
- Collaborate with suppliers to ensure raw materials meet consistent quality standards through regular audits.
- Use advanced analytical tools like spectroscopy to assess the purity of pigments and additives.
- Maintain strict quality control during storage to prevent contamination or degradation.
- Align material properties with intended applications to maximize performance and reduce waste.
The MaterialsZone Advantage:
The MaterialsZone platform provides advanced tools for raw material quality assessment and analysis—enabling data-driven decisions that enhance consistency and performance from the start.
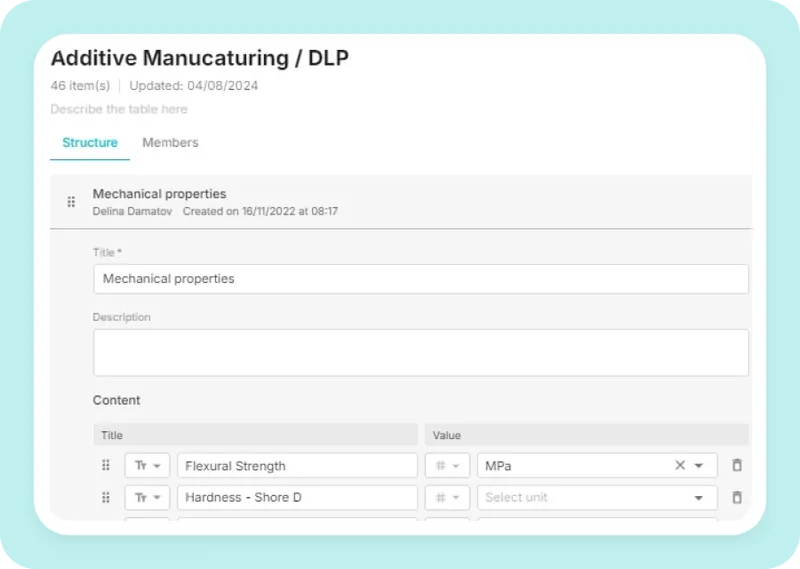
Step 2: Mixing and Dispersion Techniques
Proper mixing and dispersion are critical for achieving a uniform distribution of pigments and additives throughout the carrier resin.
This step ensures consistent material properties, prevents defects like streaking or uneven coloring, and enhances the functional performance of the final product. Advanced mixing techniques and real-time monitoring are essential for maintaining quality at this stage.
Optimization Strategies:
- Use high-shear mixers for initial blending to achieve an even distribution of raw materials.
- Employ techniques like three-roll milling or ultrasonication for finer dispersion and improved consistency.
- Incorporate in-line quality monitoring systems to detect and address inconsistencies during the mixing process.
- Optimize mixer blade design to match the properties of specific pigments and additives.
- Conduct regular equipment maintenance to ensure mixing efficiency and minimize downtime.
The MaterialsZone Advantage:
Ensure uniform dispersion and reduced waste with an AI-driven materials informatics platform that optimizes mixing parameters using historical and real-time data.
Step 3: Extrusion Process Optimization
The extrusion process directly impacts the uniformity, quality, and overall performance of the masterbatch.
Precise control of parameters like temperature, pressure, and screw speed ensures consistent material properties and minimizes production waste. Proper maintenance of extrusion equipment is essential to avoid inefficiencies and provide reliable results.
Optimization Strategies:
- Use twin-screw extruders for improved mixing efficiency and material homogenization.
- Regularly inspect and maintain screws and barrels to prevent wear and maintain optimal performance.
- Implement real-time monitoring systems to adjust extrusion parameters dynamically, ensuring consistency across batches.
- Optimize temperature profiles to match material characteristics and prevent overheating or degradation.
- Leverage data analysis tools to track and refine extrusion settings for enhanced process control.
The MaterialsZone Advantage:
Leverage MaterialsZone's data visualization and monitoring tools to obtain consistent material properties and lower production waste.
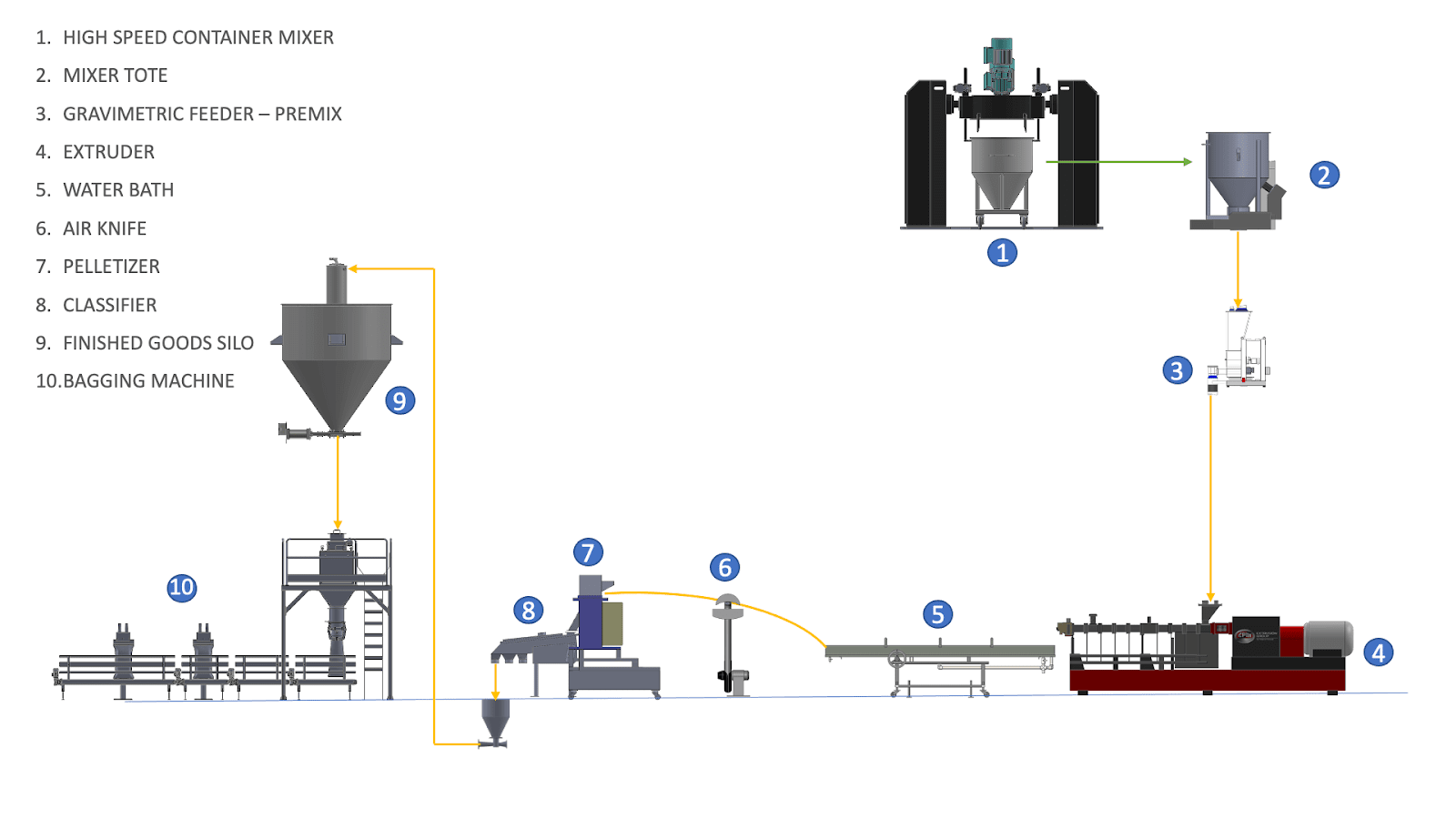
Step 4: Cooling and Solidification
Proper cooling and solidification are essential for maintaining the structural integrity of the masterbatch. Controlled cooling ensures uniform solidification, preventing defects like warping or inconsistent density. Advanced cooling systems and precise monitoring are critical to maintaining consistent quality during this stage.
Optimization Strategies:
- Use water bath or air cooling systems tailored to the polymer type to ensure optimal performance.
- Control cooling rates carefully to prevent stress or uneven solidification in the material.
- Employ moisture sensors to detect and eliminate residual moisture after cooling.
- Conduct regular maintenance on cooling systems to avoid disruptions and maintain efficiency.
- Dynamically adjust cooling parameters based on material properties and production requirements.
The MaterialsZone Advantage:
Get consistent structural integrity with MaterialsZone's real-time monitoring tools that optimize cooling parameters to prevent defects and ensure uniform solidification.
Step 5: Quality Control Measures
Quality control is a cornerstone of the masterbatch manufacturing process because it ensures that each batch meets stringent standards for consistency, performance, and compliance. Regular testing and advanced monitoring help identify and address defects early, minimizing waste and maintaining customer satisfaction.
Optimization Strategies:
- Conduct regular tests for color consistency, dispersion quality, and physical properties to ensure product standards.
- Use non-destructive methods like ultrasonic scanning to detect internal flaws without damaging the material.
- Implement digital twins to simulate and predict potential quality issues before production is complete.
- Establish robust documentation protocols to track batch performance and identify recurring problems.
- Train staff regularly on updated quality control technologies and methods to maintain high standards.
The MaterialsZone Advantage:
Leverage MaterialsZone's data collection and batch comparison tools to streamline quality checks, ensure consistency, and reduce waste.

Step 6: Process Automation and Control
Automation is essential for enhancing consistency, reducing errors, and optimizing efficiency throughout the masterbatch manufacturing process. Integrating advanced sensors, AI and machine learning, and real-time monitoring systems allows manufacturers to achieve precise control over parameters and streamline operations at every stage.
Optimization Strategies:
- Integrate IoT-enabled sensors for real-time data collection across production lines.
- Use ML algorithms to predict and prevent equipment failures with predictive maintenance.
- Implement automated dosing systems to ensure precise ingredient ratios and reduce material waste.
- Establish centralized control systems to monitor and adjust parameters like temperature, pressure, and mixing speed dynamically.
- Regularly review and update automation workflows to align with evolving production needs.
The MaterialsZone Advantage:
Enhance precision and efficiency with MaterialsZone's AI/ML-powered capabilities that enable real-time process monitoring and automated parameter adjustments.
Step 7: Sustainable Practices
Adopting sustainable practices in the masterbatch manufacturing process reduces environmental impact, lowers production costs, and ensures compliance with regulatory and consumer demands.
Incorporating recycled materials, energy-efficient processes, and waste reduction strategies can significantly enhance both sustainability and profitability.
Optimization Strategies:
- Use bio-based or recycled materials in formulations to reduce reliance on virgin resources.
- Invest in energy-efficient equipment to lower carbon emissions and operational costs.
- Implement closed-loop recycling systems to reuse production waste effectively.
- Optimize production schedules and logistics to minimize energy consumption and material transport.
- Track sustainability metrics to identify areas for continuous improvement and ensure compliance with environmental regulations.
The MaterialsZone Advantage:
MaterialsZone identifies areas for sustainability improvements with data-driven insights that track energy efficiency and waste reduction metrics that help optimize resource usage.
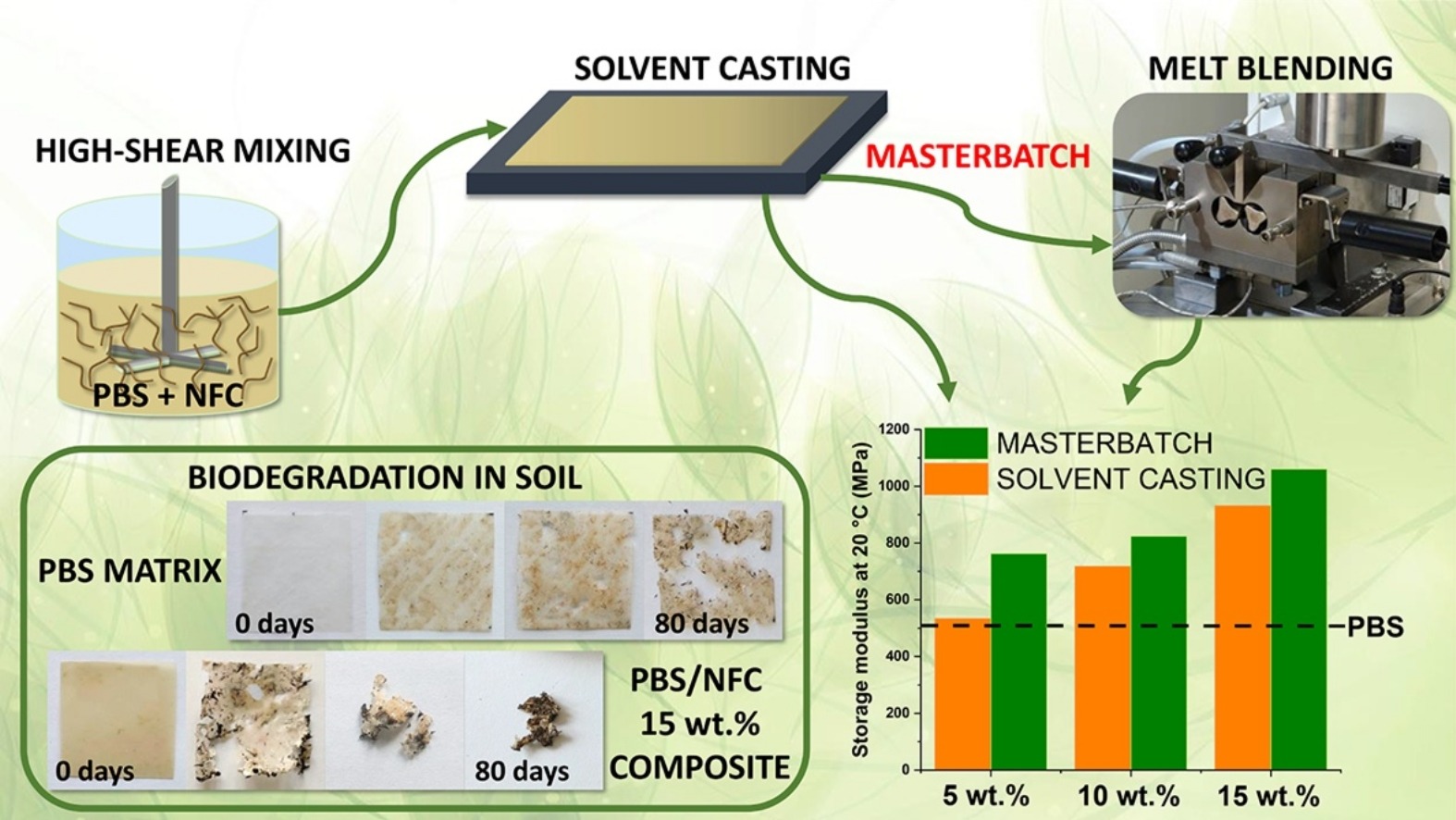
Step 8: Continuous Improvement Culture
Building a culture based on continuous improvement is essential for staying competitive and adapting to evolving industry demands. Regular evaluation of processes, integration of new technologies, and collaboration across teams ensure long-term optimization and innovation in masterbatch manufacturing.
Optimization Strategies:
- Benchmark operations against industry leaders to identify areas for improvement and innovation.
- Provide ongoing training for employees to stay up-to-date on emerging technologies and techniques.
- Encourage cross-departmental collaboration to generate diverse perspectives and creative solutions.
- Regularly analyze production data to uncover trends and refine processes.
- Invest in pilot projects to test new methods before full-scale implementation.
The MaterialsZone Advantage:
Drive consistent process refinement with real-time data insights from MaterialsZone that empower teams to make informed decisions and impactful improvements.
Get Smarter Masterbatch Manufacturing with MaterialsZone
The masterbatch manufacturing process is essential for producing materials with consistent quality and performance. Optimizing this process helps manufacturers improve efficiency, reduce costs, and meet regulatory demands, all while staying competitive in an evolving industry. With the right tools and strategies, businesses can achieve long-term success and adapt to new challenges.
MaterialsZone's materials informatics platform provides everything you need to optimize the masterbatch manufacturing process. Its advanced features include real-time monitoring to detect and address issues instantly, data-driven insights for improving workflows, and predictive analytics to reduce waste and boost sustainability.
Request a MaterialsZone demo today and take the next step in optimizing the masterbatch manufacturing process.